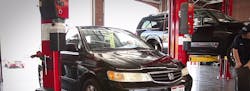
Selecting a lift isn't just about accommodating the vehicles lined up outside. Fleet managers and shop owners must factor in their shop’s physical environment to make sure their technicians, in addition to their vehicles, are well-served. Details like ceiling height, flooring material, and square footage are just some considerations that may lead a shop owner to favor one lift design over another. Whether making an initial purchase or replacing existing equipment, before the purchase – and even before deciding on a lift type – it’s important that shop owners regard their facility with new eyes and do their due diligence when it comes to finding the right lifting equipment.
“Vehicle lifts have long been one of the soundest investments a professional shop can make,” says David Shedlock, BendPak’s director of national accounts, North America. This is true for body shops, quick lube stations, car dealerships, and heavy duty service locations, in addition to general repair facilities. Because each facility varies so much in terms of size and composition, it’s important to consider every last detail.
“How a facility is laid out is a major consideration when purchasing lifting equipment,” says Megan Belt, account director at Rotary Lift. She adds the Rotary team encourages perspective buyers to take a hard look at details like available space, traffic flow, flooring, ceiling height (overhead clearance), and whether the facility is leased or owned. For example, if the service facility is leased and the installation of fixed lifts is not permissible or cost-effective, a mobile column lift might be an ideal solution to address most service operations.
Here are some more details to consider when selecting a lift (or lifts) that will best fit your space:
Measure more than once
BendPak’s Shedlock recommends that even before shopping, it’s wise to get accurate measurements and statistics for the bay or garage, including ceiling height.
“Check to make sure the garage or service bay can accommodate the fully raised height of the lift when it’s loaded with the vehicles you’ll be working on,” Shedlock says. “When it comes to two-post lifts, overhead cross bars can sometimes limit how high you can raise a vehicle. Make sure to account for the cross bar in your calculations. If the vehicle won’t fit, see if the lift is available in an extended height edition.”
Furthermore, consider how vehicles will move inside the space once equipment is installed.
“Turning radius is a factor in lift selection usually at the point of facility design,” Shedlock says. “Basically, you need to make sure that the vehicles you’re planning to service can be driven into the bay without a lot of wasted time spent maneuvering. This especially comes into play in shops with multiple bays set up along a center aisle,” he says.
Materials and mock-ups
Even the type of floor inside the facility should be examined. It’s important to assess whether the concrete floor (for example) and the ground substance beneath it can support heavy lifting equipment.
“Like everything else, concrete slabs have their weak points and strong points” Shedlock says. “After you’ve made sure that your floor can support the lift you’re considering, remember that it’s a bad idea to install it near a seam, slab edge, or directly over a tension cable. These mistakes could lead to injury or reduce the usefulness of your new lift.”
In addition, shop owners and facility managers should enlist the help of professionals who can help them to see the big picture – this includes the lift manufacturer, installer, and even a facility planner. In today’s world, there are more resources and tools than ever available at a buyer’s fingertips – resources designed to help customers feel supported through the process, and confident in this important purchasing decision. One such tool end-users can tap into is 3-D floor planning software.
Some U.S. lift manufacturers harness the help of special software to walk customers through a conceptualized redesign of their facility for 3-D visual experience. The Sweden-based ECDESIGN is one company that offers this experience. According to their site, “The ECDESIGN Repair Shop Planner [helps end-users] create a well-planned layout and maximize usage of space.” Features of the software include drawing tools, the ability to input existing drawings, 3-D models, and “walkthrough’ videos showcasing a final floorplan.
“Using 3-D space planning in the repair shop design and planning process can help ensure customers receive the best possible solution for their facility,” the company says. “[End-users can] customize the layout to maximize floor space and use equipment from automotive aftermarket companies.”
Shop smart, and safe
Knowing the dimensions of your workspace, the weight classes of the vehicles you’ll be lifting, and what features are most important to you – even before comparing brands -- will all save time in the purchasing process.
Rotary Lift’s Belt recommends prospective lift buyers consult directly with lift manufacturers for technical specifications on specific products. Together, they can determine what lift best suits the weight class of vehicles serviced, as well as any “important-to-you" product features, such as charging capabilities.
“Does [the lift] require adding 220V or three-phase power wiring to the shop, or does it operate on battery-powered 110V that can be charged with a standard outlet?,” Belt asks.
Finally, don’t neglect safety. Buyers should compare safety features and systems of all lifting products, and always look for the gold label that reads “ALI Certified” as only lifts that have passed independent safety testing can use this label.
When the research into fit, function, and features is done, it’s time to buy. But the journey to technician satisfaction and improved ROI doesn’t end there. After the purchase it’s time to work with a reputable lift installer to get the new lifting equipment up and ready to use in the bay. Many lift manufacturers use a network of third-party service teams throughout the country to help end-users with installation, setup, and support.
And after that, a consistent, closely adhered to maintenance scheduled will set the stage for success, as well-maintained equipment prevents downtime and ensures technicians are safe and productive.
Determining not merely which lifts work – but where they work – will help ensure maximum technician productivity and safety on the job.
Smart lift purchase takeaways:
· Choose the right lift for you. Consider lift capacity, clearance, foundation requirements, and whether the lift can access manufacturer-recommended lifting points on the vehicles you serve.
· Review local building code regulations. The International Building Code requires that any vehicle lift installed meet the safety standard ANSI/ALI ALCTV (current edition).
· Confirm the lift is ALI-certified. Look for the ALI Gold Certification Label
· Get help from trusted professionals. Work with experts at ALI member companies, participants, or approved distribution channels.
· Check for scams and false claims. Review the current list of Buyer Beware claims and lift certification FAQs.
· Remember the accessories. You may be able to improve a lift’s versatility with options and accessories, but make sure they’re approved for use with that specific lift.
Source: Automotive Lift Institute www.autolift.org