A path to increased productivity and fleet uptime
Only companies that consistently challenge the status quo, create new and different ways of doing things, and improve on current processes will survive in today’s competitive environment. Businesses must do so while maintaining a productive and safe working environment. And they must do so by engaging employees with responsibility, accountability, and a sense of ownership.
Lawson Products, an industrial distributor of maintenance and repair products, employs Lean Six Sigma methodology and tools to improve operational efficiency in all areas of the organization.
Lean Six Sigma
Lean Six Sigma is the combination of two process improvement methods that share the same goal. Lean and Six Sigma seek to exceed customer expectations by eliminating waste and creating efficient processes. The main difference between Lean and Six Sigma is that the root cause of waste is addressed differently. Six Sigma tactics improve efficiency by reducing variation within the process, whereas Lean methods identify and eliminate waste from unnecessary steps in the process that do not add value to the finished product or service. Both approaches are effective which is why exceptional results are gained when the two methodologies are combined.
Maintaining the workplace with 5S
5S, one of the basic practices of Lean, was key to the creation of Lawson’s continuous improvement culture. 5S, Sort, Set in Order, Shine, Standardize and Sustain, is a workplace organization method to reduce waste and optimize productivity by maintaining an orderly workplace. It can easily be implemented in all types and sizes of organizations ranging from manufacturing plants to repair shops to warehouses. A repair shop may optimize productivity with increased visibility of preventative maintenance schedules and records. Or, perhaps clearly labeled bins and cabinets filled with tools and parts, based on how your shop operates, are needed to improve uptime. Making your workplace work is really what 5S is all about. To achieve 5S success, it must be deemed as an ongoing process, not as a one-time clean up activity to satisfy management.
Lawson is dedicated to the 5S + Safety approach to staying organized. A neat and orderly workplace, one where every employee has the tools needed to get his or her job done such as printers, labels, RF guns, and scanners, is paramount to an efficient operation. Fleet maintenance managers may increase the visibility of safety signs, adopt shop floor cleaning practices with rotating employee cleanliness inspectors, and implement 5S stand up meetings where obstacles and productivity are discussed. These are just some of the many ways to make it easy for all employee functions and levels to become involved and engaged.
Optimizing inventory management
Lawson’s approach to Lean is to reduce any activity, touch or rework that does not add value. If Lawson can enhance profitability or the customer experience through replenishment, organization or custom assortments, the activity is supported.
The 5S + Safety method used internally at Lawson is also applied at its customers’ shops, parts rooms, warehouses, factories, stores, and more. Lawson representatives save customers time and money by implementing custom bin and cabinet systems to organize and add efficiency to businesses. They are placed strategically within the facility, clearly labeled and stocked with specific parts that each customer requires. Lawson representatives use a bar code and scanning system to quickly identify and reorder critical products. Through an organized approach, customers realize reduced overall supply spend while having an efficient ordering process. This means no more time lost looking for the right product, disruptive and unplanned trips to off-site stores to purchase parts or supplies, and wasted time spent taking small parts inventory -- all critical to improving fleet uptime and to ensure a safe working environment.
No matter the size or type of fleet – trucking, delivery, public utility, school buses, or tractors – Lean Six Sigma methodology and tools provide a solid foundation for creating a continuous improvement culture. When employees see that what they do makes a difference, their pride grows, their level of responsibility, accountability and sense of ownership grows. And as gains in quality, organization, optimization, customer satisfaction and profitability grow, so does competitive edge.
Content provided by Lawson Products Vice President of Marketing Liesl Abrahamson.
About the Author
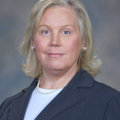