Ask the Expert: What should you know about personal protective equipment?
Q: What should employees know about personal protective equipment?
A: Physical hazards affect many people in the workplace. In the hierarchy of hazard controls, elimination is the topmost priority, followed by substitution, engineering controls, administrative controls and - the last resort in the hierarchy of hazard controls - personal protective equipment.
Personal protective equipment (PPE) refers to the protective clothing, helmets, goggles and other garments or equipment designed to protect the body of a person from injury or infection. PPE is worn for job-related occupational health and safety purposes.
The purpose of PPE is to reduce employee exposure to hazards when the engineering controls that protect workers from hazardous situations and administrative controls that lessen the threat of a hazard to an individual are not feasible or effective in reducing the said risks to an acceptable level.
PPE that is used in a workplace should be selected to minimize the risk to worker health and safety. It should be suitable for the nature of the work and any hazard that is associated with the work. It should also be a suitable size and fit and reasonably comfortable for the person who wears it.
When PPE is properly selected and used, it can effectively eliminate or minimize individual exposures to hazardous materials and physical hazards encountered in different work environments.
Hazardous materials are not limited to chemical, biological or unsealed radioactive materials or agents that pose a health or physical hazard. Likewise, physical hazards are not limited to substances, equipment or activities that can expose the person to a potential threat to their physical safety. Examples of hazards can also include extreme pressures, extreme temperatures, ionizing and non-ionizing radiation, noise and flying hazards from machining equipment.
Managers and supervisors should be aware of the reasons for providing PPE. They should also be knowledgeable about the proper usage and the level of protection PPE provides.
Employees should wear PPE in all hazardous situations.
About the Author
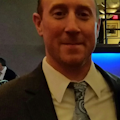