Finding your diagnostic process is critical to achieving success with vehicle service and repair. In this article, I will share many of the proven processes I have found to be successful. Some of these processes you may already be practicing, and some may provide you with a novel approach.
1. Preliminary steps
Customer interview: Gather information about the vehicle's symptoms and what led up to their existence, the history of service or repairs that may have induced such conditions, and any recent changes or events, such as extreme weather, flooding, etc., that might correlate with the current issues. For example, recently in my shop, a vehicle arrived with a complaint of many warning lights illuminated on the instrument cluster. These lights came on when the client noticed that the transmission failed to upshift after leaving a stop.
With this information, the technician began their investigation, which started with a road test to evaluate the transmission’s current state of performance. After observing normal operation, a complete vehicle health scan was performed. While examining the fault codes, we could see that the transmission control module was a source of reporting errors, which resulted in multiple modules reporting faults and annunciating via the instrument cluster. Keep in mind that since many vehicles today are equipped with active safety systems supporting driver assistance, if there are any errors in any other propulsion systems, those active safety systems will default to an inoperative condition. This is why this vehicle had the eyesight, rear automatic braking system, and other warnings illuminated.
The next step the technician took was to see if there were any applicable technical service bulletins, which there were. Following this bulletin carefully, it had a series of logical steps, such as checking the condition of the transmission fluid along with the appropriate fill level. Several other checks were also included, which ultimately resulted in a no-problem-found condition. A second interview with the client, who happened to be riding as a passenger when this problem surfaced, resulted in more information. He stated that the driver came to a stop at a light with the vehicle partially protruding into a pedestrian crosswalk. The driver placed the transmission into reverse and slowly backed the vehicle up. However, the driver failed to place the transmission back into drive. When the light turned green, the driver began to depress the throttle and observed the vehicle going backwards, and they quickly moved the shifter out of reverse and attempted to move into drive, but landed in neutral. After a couple of throttle depresses with the rpm reaching remarkably high, the transmission was then shifted into drive, and the vehicle jerked forward. This is when the transmission failed to upshift, resulting in numerous warning lights appearing on the instrument cluster.
As you can see, this additional information would’ve been extremely helpful if it had been discovered during intake.
2. Visual inspection
A visual inspection often can surface other service opportunities and potential sources of trouble. Vehicles that have numerous faults that you would categorize as extremely abnormal would call for a close inspection for evidence of the vehicle being involved in a flood. In fact, one such vehicle arrived in our service facility not long ago with numerous complaints that had us puzzled out of the gate. The vehicle was a 2019 RAM 1500 that was towed in as a no-crank, no-start; the client reported that the condition occurred while driving through a car wash.
This is what the write-up said:
Reason for customer's visit: Customer towed vehicle in. Customer states the vehicle is in a no-crank, no-start condition, and it is a salvaged title. The customer states that he drove the vehicle through a drive-through car wash, and the vehicle lost all power. The vehicle has been sitting for a month. The customer states that the wiring harness was replaced at the dealership back in 2021. This past year, the check engine light would turn on and off intermittently. A notification for the power lock system would illuminate as well. The customer noticed that if he drove the truck in the rain and hit a puddle of water, the vehicle would start to have electrical issues. Analyze and advise on repairs.
When we initially opened the hood for a visual inspection, we found a large tarp covering the back half of the engine, apparently to prevent water intrusion. (Figure 1)
After performing a walk-around inspection of the vehicle, followed by a flashlight inspection under the seats and under the dash, we could see straightforward evidence that this vehicle was involved in a flood. (Figure 2)
The next step we took was to search the Internet using the VIN, where we quickly found that the auction sale of this vehicle was as a total loss because of a flood somewhere else in the country approximately four years ago. This is where our journey stopped, and as you can see, it saved us a ton of time, allowing us to move on to more prosperous work.
Often when we have a vehicle in for a diagnostic that we have not seen before, we will sell a service that includes a comprehensive vehicle inspection. And in some cases, this inspection may be offered at no charge. In my shop, this does not mean that the technician is working for free. Performing a systematic inspection allows us to leverage the power of our shop management system to build out estimates to resolve any inspection deficiencies. These deficiencies are often documented with images and data to back up such findings.
Exterior check: Look for signs of collision damage, fluid leaks, or wear on components like tires, suspension, lighting systems, etc.
Under-hood inspection: Fluid level and condition checks, fluid leaks, loose belts, or hoses, battery cables, evidence of rodents, etc.
Interior check: Assess dashboard warning lights to ensure that all the proper lights illuminate during bulb check mode, check for unusual smells, and inspect the condition of upholstery or dash components, which might indicate electrical or HVAC issues, or, as mentioned earlier, evidence of water intrusion. Although many under-hood electrical connectors have weather protection, that doesn’t mean that they’re immune to water intrusion. With interior connections, not all connectors have weather protection. As you should be aware, moisture leads to corrosion, and intermittent electrical conductivity conditions can wreak havoc on today’s systems, especially when it comes to network communications
3. Basic checks
Fluid levels: Inspect engine oil, transmission fluid, coolant, brake fluid, power steering fluid, and washer fluid. Note color, consistency, and level, as these can indicate issues like coolant leaks or transmission problems.
Battery and charging system inspection: Check the date code on the battery; most today begin to surface failures after three years. Corrosion around the battery can lead to other faults down the road. In fact, many faults today often stem back to the basics, and that begins with a sound electrical system, which starts at the battery. (Figure 3)
4. Full vehicle scan
Health check: Many of the scan tools on the market today can produce a vehicle-wide full scan, which can be very enlightening. In fact, many of the faults that modules record do not necessarily result in annunciation to the operator; therefore, they have no clue that these faults exist. As you can imagine, this alone can help the consumer steer clear of failures down the road.
5. Diagnostic correlation
DTC to symptom mapping: As mentioned in the beginning with our “no-upshift” vehicle, many of the faults stem back to other modules reporting and/or requesting other modules to report faults. Today’s diagnostic tech needs to possess the skills to rationalize how these systems work together in concert to handle vehicle failure modes. One technique you may want to consider is creating a “mind map” that may allow you to link together probabilities. Today, there is one vehicle manufacturer that I’m aware of that has such a tool inside its diagnostic application. Tesla has a section within their diagnostic toolbox called Sandbox.
This tool allows you to add current vehicle system faults and see how they correlate to other faults, which are often linked to technical documents that may uncover potential inspection points along with the resolutions. Look for future technical articles covering this topic in depth. (Figure 4)
Mileage correlation: Consider time or mileage-based maintenance items that may have been overlooked and or timed out. Catching up on maintenance can sometimes resolve drivability problems.
6. Preventive maintenance recommendations
Using manufacturer guidelines: Reference the vehicle manufacturer's maintenance schedule to tailor recommendations, ensuring they align with warranty and service expectations. Beware, in some cases, you may not find recommendations for services that would logically support long vehicle life. For example, transmission and drivetrain fluid services may be recommended, but their intervals are often found to be excessive, in my opinion. You, as a service professional, should establish recommendations based on your experience. In my service facility, we are seeing more and more Tesla vehicles, and we are finding that the drive units, aka traction motors, aka electric machines, don’t have a fluid change interval recommendation from the manufacturer.
We are finding that at around 50,000 miles, the drive unit fluid is extremely dark. On dual motor vehicles where the rear permanent magnet drive motor is the one with a higher duty cycle, we’re finding its fluid much darker than the fluid that gets drained out of the front induction motor unit. Both units have spin-on oil filters and require special fluid. You will also find a special process needed to properly fill these drive units, which involves operating the oil pump to dynamically fill the drive unit. We are now recommending fluid changes well ahead of 50,000 miles.
7. Documentation and reporting
Record keeping: Document all findings, as mentioned earlier, our shop management system allows us to clearly document all inspection items and maintain those records for future reference.
Customer communication: Clearly explain findings, potential causes, and the rationale behind recommended repairs or maintenance. Use simple language or visual aids if necessary. There are many visual aids available, such as MotoVisuals (Figure 5), which is what we use in our shop. The automobile is a complex machine, and this application and its animations make it a great educational tool and ultimately help us to maintain the client's vehicle.
8. Follow-up
Post-repair verification: After service and repair, one should extensively road test the vehicle and exercise the systems on the vehicle. In some cases, recording vehicle data showing a return to nominal values can go a long way in establishing professionalism and credibility. In some cases, a single repair doesn’t necessarily mean that all vehicle symptoms will be eliminated. (Figure 6) Post-repair verification analytics can help to prove that your repairs are moving the vehicle in a positive direction.
9. Quality control - QC
QC should exist at every step, work orders should have an inspection line for communication. The checks required for one of our job packages include the fluid levels, wiper system, air filters, and more.
In our facility, every work order has a quality control step that must be completed before we are allowed to close a work order. Most, if not all, drivability-related repairs will include an extensive road test with recorded vehicle data. This provides us with a method to obtain data showing proper vehicle operation and is often used to complete OBD-II monitors and document these. As you are aware, many vehicles with permanent DTCs need to be driven so that the diagnostics internal of the ECM can be run so that these permanent DTCs will self-clear.
Within this article, we discussed numerous best practices that can help you fine-tune your diagnostic process, which can ultimately lead to increased sales and profitability. Moreover, following many of these steps can lead to improved customer satisfaction and demonstrate technical proficiency and overall service professionalism. This goes a long way towards building strong credibility for you and your profession.
About the Author
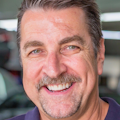
Scott Brown
Founder - Diagnostic Network
Scott is an ASE Master Certified Automobile Technician with L1, L3, & L4 credentials and has over 39 years of professional service industry experience. As an independent shop owner in Southern California and with his engagement at various levels of within our industry, he continuously strives to move the industry forward through networking, education, communications, and training. Scott is a founder of the Diagnostic Network (https://diag.net/) which was born in 2018 after he retired after 22 years at iATN, where he served as company president.
Brown is also the host of Professional Tool and Equipment News (PTEN) and VehicleServicePros.com podcast, Torque Factor. The podcast addresses the latest automotive service technologies while focusing on expanding knowledge and awareness around tools, equipment, education, and industry trends.