Hybrid and HV electric challenges
Case study: 2011 BMW 750Li N63 4.4L V8 F04 Active Hybrid (126,000 miles)
This 750Li was towed in as a no-start from another shop (who received it from a BMW dealer). BMW’s ActiveHybrid vehicle uses a unique system that looks a bit different than most hybrids. One of the main differences is that the heart of the system (the HV battery) is laser-welded and cooled by air conditioning (Figure 1). The HV battery consists of 35 lithium cells that produce 3.6V each, for a total of 126V.
BMW uses a 30/80 percentage state-of-charge strategy. When the charge is under 30 percent, a Check Control message will be displayed to alert the driver. This HV lithium battery houses an ECU, electromechanical switch contactors, connectors for the HV and low voltage cables, connections for refrigerant, and a vent. The HV battery encompasses an IBS (Intelligent Battery Sensor) that measures HV voltage, charge, and discharge current along with battery cell temperature. This information is important to understand, since this component is the most probable cause of the no-start condition.
After scanning the F04 BMW using ISTA (the BMW factory scan tool), multiple codes were retrieved (Figure 2). It was apparent to me that even though there was an abundance of DTCs, they all had something in common, the HV battery. The code descriptions ranged from “battery cell low,” “cells differ from each other,” “connections between cells,” “measurement issues,” and a “deactivation fault.”
The first DTC we would begin our approach with was the high-voltage state-of-charge. Because this DTC could cause the no-start condition, we knew that we had to get the HV battery charged up, or the MG (motor generator) would not crank the ICE (internal combustion engine) over. Not being all that familiar with this system, I thought I would RTFI (read the friggin’ information) from the BMW website. What I uncovered was an in-depth description of the system and how it operates.
This BMW Active Hybrid utilizes a specially tuned ICE N63 V8 engine that generates 450 horsepower that is coupled with an electric motor located between the engine and the transmission (Figure 3- see opening image). This is similar to Honda’s IMA (Integrated Motor Assist) single MG. The electric motor adds another 20 horsepower to the overall power output. The MG is powered by a special lithium battery pack that is located in the trunk and cooled by the air conditioning system. Just like the more common Honda IMA hybrid system, this hybrid does not use a conventional starter motor, but rather, uses the MG to start the ICE up.
BMW states that the coupling of the ICE and MG produces the performance of the BMW V12 motor while only consuming the fuel of a 6-cylinder engine. Get this: under heavy acceleration this BMW sedan can accelerate from 0 to 60 mph in 4.7 seconds, making it a "driving machine," as BMW likes to call it. Just like all hybrid vehicles, it uses Start-Stop technology. This all contributes to less fuel consumption.
For me, reading through the BMW information is sometimes like trying to understand the Greek alphabet. An example is their acronym SME (battery management electronics), which is not what I would expect. After decoding the acronyms, I was able to make more sense out of the information. This important step helps build my “game plan” from the information gathered. If I were to skip this step, it would likely lead to a misdiagnosis of the vehicle.
Becoming one with the vehicle
BMW, like most vehicles we work on, uses a CAN (controller area network) system that operates using the EME (electric machine electronics) control unit. This EME performs the primary (master) role, while the SME control unit is secondary. Associated commands are transferred via the bus signals on the CAN network. The EME control unit provides the request to start the high-voltage system when either terminal 15 is switched on (like “Ignition ON”) or there is a request for air conditioning from the HV system.
When a start request is initiated, if the bus signals are good, and the high voltage interlock loop is closed, the following will take place. The system runs a test on the high-voltage electrical system by raising the voltage then closing the contacts of the switch contactors. Open contacts protect the link capacitors in the high voltage circuit that switch on current flow. This prevents permanent damage to the link capacitors and the switch contactors.
The voltage flow is as follows: The negative lead of the switch contactor is initially closed, followed by a constant current in the positive lead via an electronic circuit (to charge the link capacitors). This allows the voltage in the high voltage electrical system to increase within milliseconds to a value that is slightly below the voltage of the high voltage battery. When that process is completed, the positive lead of the switch contactor is closed. This information is then provided to the SME control unit that communicates if there was a successful start (via the CAN-bus) to the EME control unit. All faults are sent the same way and will signal a no-start condition, as we encountered on our ‘Bimmer.’
If this sounds familiar, it is because the Toyota Prius HV system has been around for years and uses a similar pre-charge resistor whose job is to protect the SMR (system main relays) from burning up. Again, I would like to point out that all hybrid, extended-range, or EV vehicles use similar components that work the same way but are packaged differently.
Game plan established
Moving on after reading the BMW HV system information, we were now able to build our “game plan” and proceed. We uncovered a low HV battery charge that was no different than what we have seen on numerous hybrid vehicles. We had a conversation asking the vehicle owner when the no-start initially occurred, and we were informed it was months ago. Now it was starting to make sense, as the BMW display had an alert of a no-start along with a warning message on the dash cluster.
With the HV battery below the recommended level, the BMW procedure to get the HV battery up and running had to be performed. The recommended procedure is to connect an AGM battery charger that can provide at least 13.5 volts with a maximum current rate of 70 amps to the 12-volt AGM battery. In turn, the charging procedure provides voltage to the DC converter that starts charging the HV battery. BMW information states that its system will initiate a charging procedure (which takes about 20 minutes to provide enough voltage to the HV battery) to enable the ICE to crank over. Once the HV battery is at a proper level to crank/start the ICE, there will be a yellow symbol and text message in the display.
As we noted on the vehicle’s dash display, it confirmed that the high voltage battery was low on charge, indicating a 5% level (Figures 4+5).
Considering the system description information we already reviewed, we decided to try charging the high-voltage battery (via the vehicle's system) from the dash display. We attached our Fronius battery charger/maintainer, as suggested in service information, to allow the HV battery to charge up. Unfortunately, this procedure was not able to get the HV battery up to the proper charge level to start the engine. If the HV battery is discharged and deteriorated to a very low level, the easy charge procedure I just described will not work.
To verify that the HV battery was in fact down for the count, we needed to perform a few more tests. The recommended procedure for the HV battery de-energized state is not verified by using a CAT III voltmeter or the BMW factory software ISTA, but instead the vehicle’s system that measures itself. These measurements of the high-voltage system are analyzed by the internal components that transmit the measured readings (via the bus system) to the instrument cluster.
The instrument cluster will not generate the Check Control message to dash display unless it determines (from internal testing measurements) that all high-voltage components consistently signal a de-energized state. Keep in mind that if the HV battery voltage level goes excessively low it may not be able to be recharged using this procedure. On this vehicle that was exactly the case. No matter how many times we tried, the HV battery would not accept a charge and was now down to zero percent (Figure 6). Since this was the problem, the HV components such as the converter, motor-generator, and wiring had to be checked for proper operation.
Diving in deep
Now we had to change our focus and start checking the HV components where safety precautions come into play. While working on most Euro vehicles that are either hybrid or full electric, there is a warning while using an OEM scan tool (Figure 7). The BMW scan tool warning states that only a trained qualified technician should be working on the HV system. This warning must be taken seriously and is especially important; remember, it’s not your father's Oldsmobile. It contains high voltage that can cause a severe burn or even death. Working on high-voltage systems can be dangerous to the underqualified individual who does not have the proper training and equipment. I would suggest getting yourself into a hands-on hybrid / EV class (not just a seminar), so you can receive the proper training.
Following all the safety precautions, we started our journey checking the components. We focused especially on the voltage going to the converter. The incoming converter voltage was found to be in the recommended range, but the HV battery was still not able to accept the charge. Was it a bad converter? Wiring? HV Battery? Leaving no stone unturned, we made sure that all the wires from the EME / MG (located between the engine and transmission), along with the HV connectors that go to the HV battery in the trunk, were operational.
We disconnected the connectors from the MG and HV battery, then connected our Fluke 1587 megohm meter, confirming the wires were good. The next connection to check was the HV interlock switch that is in the trunk (Figure 8). This was a very easy component to check, since all that was needed is to disconnect it and then check its continuity with an ohmmeter.
The contactors were not going to be that easy since they are in the HV battery case. To test the HV battery contactors, we had to rely on scan data that provided information on battery cell and contactors issues (Figure 9). Before making our ultimate decision, I thought we should try to reprogram the SME just in case there was a chance it may change something. The programming was easy to perform, but unfortunately, it did not make a difference. With all the possibilities considered, the consensus was that the HV battery was defective and had to be replaced.
We called the BMW dealer to get a price on the HV battery and were told it was about $15,000, plus a core charge. I called the BMW owner to give him the information and pricing for the repair. The owner's first response was that it was such a beautiful machine he was going to approve the repair, then hours later, he changed his mind and said he would get back to us.
I received a call the following week telling me that he researched a company in California that rebuilds those batteries for much less. I thought it was too good to be true since BMW and Mercedes Benz are the only companies that use this laser-welded type battery. The owner provided me the name and number of the rebuilder, so I Googled them to check them out before calling.
The rebuilder said that they needed the old battery and $8,500 before they would send a rebuilt battery out. When I asked them about the warranty, I was told it was 90 days, making me believe that they most likely were not the best quality reconditioned batteries.
The Google research provide me with pictures and information of their repair shop that reconditioned mostly Toyota batteries along with customer reviews that were far from stellar. I called the vehicle owner back to share what I had uncovered, allowing him to make the decision not to purchase the battery. I was glad the active hybrid owner had listened to me, and I awaited his next course of action.
After a few days, he called and said he found a reconditioned battery on eBay that had a good return policy and was priced at $3,500. I stated that most likely it was not going to be a good battery, but I could not convince him otherwise. About a week later, we received the reconditioned battery and compared it to the original (Figure 10). Take a look at the BMW original to the left, and the reconditioned one to the right. Notice anything? You bet, look at the welding job on the OE versus the reconditioned one.
I told the vehicle owner he would have to pay for the labor, whether the HV battery he purchased worked or not. I explained that we had to recover the A/C system’s refrigerant and remove all the other connections, then install the reconditioned unit and evacuate and recharge the A/C system, followed by programming it. Remember, since this system is on the CAN-bus, we had to make sure the VIN was programmed in the HV battery, along with the latest updated software.
The verdict is in
After our install, AC evacuation, recharge, programming, and HV battery recharge, the replacement battery level would not change from 16.75 percent. The HV battery percentage state of charge to start the ICE needs to be about 25% or more. We tried the recharge procedure on the replacement battery multiple times, which failed due to a relay issue.
Since it did not work, the BMW owner wanted us to remove the HV battery and install the old one back so he could return it. In the meantime, he decided not to go ahead with the repair and towed it to the BMW dealer to trade it for a new (non-electric) ‘Bimmer.’
It’s a bummer not seeing a vehicle through the final stage of repair, but it’s not my decision to make. Luckily, I found out through a tech at the BMW dealership, the HV battery was replaced, and the vehicle was running. I felt better knowing that my diagnosis was correct; I just felt robbed of the opportunity to repair the vehicle.
Information on any vehicle is key to providing a proper diagnosis and repair. Hoping this article provided you with some insight on how different this HV system is, but not.
About the Author
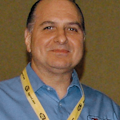
G. Jerry Truglia
Jerry Truglia, also known by "G," is an automotive instructor and author whose work with the US Environmental Protection Agency, Society of Automotive Engineers, National Automotive Service Task Force, Council of Advanced Automotive Trainers, Motor Age and Motor Age Training, Professional Tool and Equipment News, and the not-for-profit Technicians Service Training has made him nationally recognized in the automotive repair industry. G. is an ASE World Class Triple Master Technician Auto, Truck & School Bus, L1, L3, F1, A9, X1 C1. Connect with him at LinkedIn.