Turbocharger diagnosis and maintenance
In the year 2025, the Environmental Protection Agency will require automakers to produce cars and light trucks that get an average of 54.5 mpg. Small four and six-cylinder engines will replace large V-6 and V-8 powerplants and will be super-efficient with complex systems like start-stop, variable compression, hybrid configuration technology, and turbocharging.
Some current and next-generation gasoline and diesel engines utilize turbo technology to meet global emission requirements, reduce powertrain weight, and provide power equal to or better than larger engines. In 2021, 38 percent of all new vehicles sold in the U.S. had a turbocharged engine. According to IHS Markit (a team of data scientists, financial experts, and industry specialists), turbocharger production will increase significantly from the present to 2025. Your customers will require service and/or have questions about the turbo under their hood.
A turbocharger is an exhaust-powered, centrifugal air compressor that forces air into the engine, raising the intake manifold’s pressure — also called boost. The compressor is powered by recycling some of the heat energy that is normally lost to the engine’s exhaust system. For example, burnt gases in an exhaust manifold at a temperature of 1200°F vs. the temperature of the exhaust exiting a turbocharger’s turbine at 700°F. This temperature differential of 500°F represents the energy recovered by the turbocharger to be converted into mechanical energy powering the turbo’s compressor.
Invented in the early 1900s, turbos were widely used starting in the 1930s on aircraft, off-road equipment, and heavy trucks. They became popular in automobiles in the mid-1980s, and because of the 1979 gas crisis, many manufacturers tried to utilize them to essentially make small-displacement engines have the power output as a larger engine while getting the same fuel mileage as small engines. Some automotive applications were successful, like the Saab 900 Turbo (fuel- injected) and the Mercedes-Benz 300TD (diesel) and others not so much, like Ford’s first effort at the 2.3 turbo Mustang and Buick’s early turbo models, both with carburetors — a technology that did not work well with turbocharging. Today with microprocessors controlling everything attached to an engine, turbochargers are fully integrated into electronic engine management systems and work seamlessly to produce engine efficiency and power that was promised in the 1980s but only seldom delivered.
Lacks power or poor acceleration
Most owners of turbocharged vehicles know that something is wrong when their car or truck either lacks power on acceleration and/or does not produce normal boost pressure. Lackluster engine performance could also be accompanied by a check engine light and OBDII codes PO299 (Turbo/Supercharger Underboost Condition) or PO234 (Overboost Condition).
Two common causes for a P0299 are a malfunctioning wastegate or a faulty boost sensor. A stuck, or leaking wastegate will cause exhaust gases to bypass the turbine, not allowing it to fully power the compressor to make it boost. A bad boost sensor can under or over-report boost pressure to the ECU, causing it to set the code. If a diverter valve or wastegate fails to open a code P0234 can be set. The main criteria for the code to occur is when boost pressure exceeds a pre-determined level for more than two seconds. Depending on the manufacturer, engine RPM and ambient air temperature are also taken into consideration when setting the code. When an over-boost condition is detected, the ECU can enter “limp-in mode” and restrict engine rpm.
Poor engine performance and/or turbo-related DTCs are too often blamed on the turbocharger, which is only at fault about 20 percent of the time. To avoid comeback repairs and keep your customers happy, the root cause of a turbo-related issue needs to be diagnosed. While a turbocharger is a precision-balanced, high-tech piece of machinery, its operation is simple and only requires four things to function: 1) sufficient exhaust gas temperature; 2) non-restrictive supply of air; 3) minimal exhaust system restriction and; 4) clean oil supply and evacuation.
Turbo/engine maintenance
When Garrett AiResearch Industrial Division (now Garrett Motion Inc.) started mass-producing turbochargers for the automotive market in the mid-1980s, there were an abnormally high number of warranty claims for failed turbos. Before this, turbochargers were considered a highly reliable, low-maintenance item that could typically go more than 300,000 miles in diesel engine applications without any problems.
What had changed? The answer turned out to be simple — the maintenance habits of automotive vehicle owners were vastly different from those of fleet owners of heavy-duty trucks. Up until the 1980s, turbocharger production was almost exclusively for the diesel truck and heavy-duty, off-road vehicle markets. Skipping, or taking shortcuts regarding engine maintenance on engines that cost as much as $40,000 is not cost-effective, and maintenance schedules for these fleets of vehicles were strict in that they were performed on time and with quality parts (filters) and lubricants. This was not the case in the automotive market, where the mindset of most automobile and light truck owners regarding maintenance is “I’ll get around to it when I can.” Or, “I don’t take my car to the shop unless there is something wrong with it.” While an engine may survive this lack of maintenance for a time, a turbocharger does not.
Turbocharger lubrication
Dirty oil due to lack of regular oil changes, the wrong type of oil, low oil levels and not changing the oil filter all can contribute to turbocharger failure, as they are especially sensitive to lubricating oil conditions. The center housing rotating assembly (CHRA) contains the turbine shaft wheel, compressor wheel, bearings, and seals. The rotating components within the CHRA reach speeds of between 60,000 and 300,000 rpm under full-boost operation. The rotating parts are finely balanced and float on a thin film of engine oil. With tight clearances between the turbine shaft bearings, impellers, compressor, and turbine housings, plus high bearing surface speeds, it doesn’t take much oil contamination to cause turbo failure.
Don't overlook the condition of engine oil as a cause for turbocharger damage. Does the oil at the end of the dipstick look dirty? Does it have a milky, foamy, and/or a cream-color to it, or does it smell like gasoline or diesel fuel? A coolant leak, worn piston rings, or leaking fuel injector can contaminate engine oil enough to damage turbocharger bearings.
What type of oil should be used in a turbocharged engine is always a contentious debate in online forums. General recommendations are semi-synthetic, or fully synthetic oil with SAE weights of 5W-30 or 0W-20 for gasoline engines and 5W-40 for diesel applications. Oil recommended by the vehicle's OEM is always the best type to use in a turbocharged engine —after all, a hundred product liability lawyers can’t be wrong!
Supplying clean, filtered oil to a turbo is important and draining it back to the oil sump is equally so. As oil circulates between the turbine shaft, bearings, and center housing, the air gets mixed with the oil, causing it to turn into a substance that appears like brown whipped cream. The foamy oil uses gravity to flow down the oil drain at the bottom of the CHRA and into the engine's oil sump. Restrictions or blockage that prevents the gravity drain from functioning will cause the oil to remain in the CHRA, possibly creating leaks in the compressor and turbine housings. Compressor housing leaks are more common on gasoline engines because they are periodically exposed to intake manifold vacuum.
Under full boost, an engine’s piston ring blow-by can cause turbo seal leaks if the crankcase vent system is partially clogged, especially from engine sludge in winter under cold operating conditions. This can cause positive pressure to build up in the crankcase, restricting the flow of oil from the turbocharger drain. A dirty air filter that creates a restriction resulting in a pressure drop between outside air pressure and the turbocharger compressor inlet is another cause for oil leaks. The restriction is not an issue when the engine is under load, as positive pressure exists at the compressor seal. However, during idle or low-load conditions, this partial vacuum can cause oil to be sucked from the CHRA bearings, through the seal, and into the compressor housing.
Intake and exhaust plumbing
Air leaks in the compressor outlet plumbing, intercooler, throttle body, or intake manifold can all cause low turbo boost and poor engine performance. During a test drive, if whistling noises are coming from under the hood, it’s likely due to compressor/intercooler or exhaust/turbine leaks. A condition called “overspeeding” can be caused by leaks between the compressor and intake manifold, where the turbo has to work harder (rotate at speeds beyond its design limits) to overcome the leak. It can also be caused by aftermarket engine fueling modifications; wastegate or VNT mechanism set incorrectly; electronic wastegate sensor malfunction and installation of an incorrect turbocharger. Spinning a turbo beyond its design capabilities causes severe damage to the compressor wheel and other components.
A damaged/missing air filter can allow small particles of dirt to end up in the compressor, damaging the compressor impeller (wheel). Dirt (and especially sand) will erode the edges of the blades on the compressor wheel. The compressor blades should come to a sharp point. If they are rounded off (even slightly) or have a saw-tooth abrasion, this indicates dirty air entering the compressor housing. As the blades erode, the compressor loses efficiency and the turbo boost will suffer.
Leaks between the exhaust manifold and the turbine inlet will not allow enough heat energy to enter the turbine, affecting compressor performance. Turbocharger turbine performance is sensitive to exhaust backpressure, and a restricted catalytic converter will reduce the amount of heat energy the turbocharger can absorb to spin the compressor, causing low boost conditions. On diesel applications, a clogged diesel particulate filter (DPF) can also lower turbo boost.
Turbocharger quick inspection
When faced with a low boost, or an engine that lacks power on acceleration conditions, technicians are faced with a dilemma. Turbo performance affects engine performance, and poor engine performance affects turbo performance. In this “chicken-before-the-egg” scenario there is about an 80 percent chance that the turbocharger is not at fault. Engines that use a turbocharger are subject to all the things that can (and do) go wrong with engines that don't use a turbocharger. For example, low compression in one or more cylinders caused by valves not sealing or worn piston rings; restricted catalytic converter; bad fuel injectors (diesel or gasoline), and ignition system faults will all cause poor engine/turbo performance.
If the turbocharger is producing low boost, a quick inspection of turbo bearings and wheel-to-housing clearances can be checked using your fingers. Pinch the compressor wheel mounting nut and put pressure on it in any direction while rotating it slowly. The compressor wheel should turn freely without binding. There should be a normal amount of up/down “play” but if you can feel the compressor blades rubbing on the housing, the bearings are bad. A visual inspection of this condition will show flat edges on the compressor blades where they are rubbed on the housing. This test also works on the turbine/exhaust side of the turbo.
If a dial indicator is available a somewhat more accurate bearing clearance check can be performed. With the dial indicator mounted on the oil inlet, position the plunger against the turbine shaft to measure bearing free play. Up-and-down shaft movement should not exceed 0.003” to 0.006.” Shaft endplay (in-and-out movement) should be in the 0.002” to 0.004” range. These specifications are “ballpark” numbers, and a factory service manual should be consulted for actual measurements.
If you determine that a vehicle’s turbocharger needs replacement, finding the root cause of the failure and providing customer advice on driving habits and automotive maintenance will go a long way towards not repeating the process in the future. Check out the sidebar on Turbo Replacement and Operating a Turbocharged Vehicle.
Turbo replacement and operating a turbocharged vehicle
When replacing a turbocharger, it’s a good practice to find out why it failed. The turbo is an expensive part ($600 to $2,500+) and is often difficult to remove/install. If the new unit fails in a few thousand miles, the vehicle will be back, along with an unhappy customer. Once the turbo is removed, take a close look at why it failed. If the compressor wheel blades are rounded off, inspect the air filter and ducting. If either the compressor or turbine wheels show signs of blades rubbing on the compressor/turbine housings, or if blades are broken, suspect a lubrication problem or foreign object intrusion.
Turbochargers are not difficult to take apart, and inspecting internal parts can help to determine the root causes of failures. Remove the compressor housing (easy) and the turbine housing (maybe rusted—use a hammer). Remove the compressor nut and wheel and pull the turbine shaft wheel out of the center housing (CHRA). Look for indications of heat damage (yellow or blue color) or scoring on turbine shaft bearing surfaces caused by: dirty oil, low oil pressure, carbon deposits inside the CHRA, and/or a blocked/restricted oil drain tube. An often-overlooked cause of lack of lubrication is a blocked oil inlet. Oil in the oil feed pipe to the turbo may have been "cooked" due to repeated hot shutdowns and carbon deposits can block the feed line. Replacing the oil inlet pipe is a good practice when replacing the turbo. If the turbo has a water-cooled CHRA, check the water lines for restrictions. If compressor wheel blades are broken off, check the compressor ducting and intercooler for turbo-shrapnel as part of the replacement.
If a turbocharger replacement is needed, consider using a quality aftermarket supplier as a cost-effective alternative to a new OEM unit. Melett Limited (www.melett.com) is based in the UK, with worldwide distribution to over 100 countries, including through Melett North America, Inc. located in Memphis, Tennessee. The company offers replacement turbochargers (includes gaskets and fasteners), center housing rotating assemblies, and individual repair parts to the independent aftermarket. The Melett website has extensive information about turbocharger failure diagnosis, including detailed explanations, photos, and videos.
In addition to explaining why their turbo broke, offer your customers advice about turbocharged engine operation and maintenance. Oil temperatures on a cold engine are not ideal for turbo lubrication. No pedal-to-the-metal driving until the oil is warmed up—only takes a few miles. More of an issue for light truck owners that pull heavy trailers, shutting down the engine right after hard driving can cause carbon build-up inside the oil feed line and CHRA, damaging turbo bearings. Let the engine idle for a few minutes to cool oil temperatures before turning it off (not applicable for water-cooled turbos). If the oil on the dipstick looks like it was last changed 12,000 miles ago, tell your customer in the nicest possible way that they should consider more frequent oil changes. The vehicle owner’s manual will address all of these issues and if your customer doesn’t have one, they can be found online. Print out the pages about turbocharger care and attach them to the work order.
About the Author
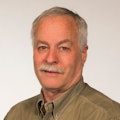
Tracy Martin
Tracy Martin writes for Motor Age, Aftermarket Aviation Defense, Contact! and Turbo Diesel Register magazines. As an ASE certified master technician and consultant, he has worked in the automotive aftermarket for over 25 years and has provided consulting services for Snap-On Tools, Sun Electric, Chevron Oil and Nissan of North America. He has developed automotive/powersports curriculum and taught courses including: engine performance, automotive electronics, fuel injection, ABS braking systems and advanced motorcycle riding techniques. He has also provided consulting services as an expert witness for automotive and powersports-related court actions.
He is the author of five books: How to Diagnose and Repair Automotive Electrical Systems, Motorcycle Electrical Systems–Troubleshooting and Repair (two editions), How to Use Automotive Diagnostic Scanners (two editions) and How to Modify Motorcycle Fuel Injection, all published by Motorbooks International.