Delivering professional automotive repair and service
Automobiles are one of the most sophisticated devices most humans will ever interact with. That comment came from Dr. John Heywood, a mechanical engineering professor at the Massachusetts Institute of Technology. He was an instrumental figure when it comes to perfecting the modern engine design technology that we see in automobiles today.
In 2018, Heywood was interviewed at an SAE event where he said “Cars are everywhere. They’re one of the biggest, most complicated products we use every day.” If you think about that statement for a moment and let it sink in, you’ll realize how critical your job is at solving problems when these sophisticated products experience failures.
Drowning in data
If you’re going to utilize the volumes of information needed to accurately address a vehicle’s problem, access to digital service information is paramount. Knowing how to search through a database like this is the first part of the challenge. Being able to also accurately reference and scrutinize that information and apply the effective repair methods to vehicles is equally challenging. Additionally, scan tools and other diagnostic devices are needed to communicate with these complex machines.
While we have many choices of equipment options, several tool companies are continuously developing products that are never 100 percent complete when they hit the market. For many of these companies, when they embark on developing a tool, they need to make significant investments in a number of areas to provide a viable tool for the marketplace. For the most part, software development for these tools is continuously advancing, and when these companies decide to enter the market with their product or service, they usually have to figure out how they’re going to fund the continuous development of these products. In most cases, a software subscription model is usually chosen. We’ll go more in depth on this topic later in this article.
Service information
While there are numerous aftermarket service information platforms out there, one needs to really analyze and challenge the information offered when using it to apply a repair to an automobile. In my shop, we have access to multiple information resources including aftermarket and OEM information services. It would be nice if there was a single location that had all of the most up-to-date and comprehensive information available but that simply does not exist due to the complexities involved in our field.
In most cases, aftermarket service information platforms source their information directly from the vehicle manufacturers. This information is usually licensed from the OEM. For the most part, the information is gathered, parsed, and then re-published. However, you may realize that there are many potential failure points along the way. Even the OEM at times can have a mistake or the wrong information published with service literature. Fortunately, we’re all living in a digital world today which means updates can occur at any time. Now, this could be a good thing but could also mean that there could be some latency in accuracy with that service information depending on your source.
For example, I recently discovered where Toyota made an update to the requirements calling for a lane camera calibration. Prior to July 2020, the service literature stated that if a toe-in adjustment had occurred on the vehicle, then a lane camera calibration process would be required. If one is accessing the factory service information that’s included with the Toyota Techstream subscription, one would have access to the latest information available. However, if you accessed this information in an aftermarket resource, you may be reading the old information.
Case Study
On July 27, 2020, a 2014 Toyota Highlander Hybrid arrived in my shop for new tires and a wheel alignment. I advised one of my service writers to research the post wheel alignment requirements since this vehicle was equipped with all of the advanced driver assistance features available for that vehicle. He first performed the research within one of our aftermarket resources. This resource, like many, source their information right from the OEM. For this particular query using “lane camera” as the search term, he found the following language within the Caution/Notice/Hint section stating: “If the lane departure warning camera is replaced or removed and installed, or the toe-in is adjusted, perform lane departure warning camera adjustment.”
Reading this language is pretty straight-forward, which basically states that if you perform a wheel alignment and a toe adjustment is required, a lane camera calibration would be a required service. Normally, we would have just proceeded to recommend and perform the service operation but we weren’t sure how much labor was required for the lane camera operation and decided that we would place an inquiry to the local dealer in order to get an idea of what the costs for a wheel alignment and ADAS calibration(s).
When we contacted the local Toyota dealer and asked them for an estimate on a wheel alignment and a lane camera calibration, the service advisor we chatted with advised us that the camera calibration is only required if the vehicle was in a collision or if the windshield was replaced, but not in the case where the vehicle has a wheel alignment. To me, this information seemed new, so we wanted to know more.
We proceeded to double check with Toyota’s factory service information by looking up the same lane camera operation in Toyota’s Technical Information Service (TIS) and found a Document ID: RM100000000CGYL with a release date of July 17, 2020, version 6.10:8.0.50.
Although the wheel alignment operation calls for a Lane Camera Calibration, when we look at the Caution/Notice/Hint section within the Lane Camera Calibration document, the language that once talked about wheel alignment has been removed. What does this mean for the repair professional? If one had only landed on the lane camera calibration document and relied solely on that information alone, the vehicle service paths may have taken different routes depending on which version of the document you referenced. What did we do? We decided to include the camera calibration process as part of the overall service we provided to the customer during this visit.
Diagnostics
Given that the state of our vehicle market is primarily driven by electronics and managed by software, many vehicles today are repaired by updating the software found within certain modules on the vehicles. If you’ve been involved with repairing vehicles over the past decade, there’s no doubt that you’ve already encountered a vehicle in your bay that needed some sort of software update. Depending on your situation, you may have experienced little to no difficulty with performing the required software update.
Today, in my opinion, a modern service center in pursuit of delivering expert service must consider budgeting access to multiple software solutions, whether they be for access to service information, diagnostics, support, or module programming operations. When it comes to choosing your diagnostic software programs, you should be aware that it takes a significant commitment for a company to properly license and develop their offering. I reached out to the Equipment and Tool Institute (ETI) and spoke with Greg Potter, CTO, and Brian Plott, executive director, in order to gain a little perspective on what it takes for a scan tool company to begin developing their products.
Brian reported that the outlay for one year of data licensing may run in the ballpark of $75-125,000 which would cover approximately 90 percent of the car parc. From there, the company could then begin developing their product so it can be packaged and distributed to the market. As you can see, it takes a substantial investment and commitment by these companies to even begin developing scan tools to help you do your job. Please keep this in mind when you’re looking at making an investment in a diagnostic scan tool.
Subscriptions
A subscription model is becoming more commonplace nowadays and from what was mentioned earlier, it makes sense but I wanted to take a moment and distill this a little further. For those of us in the service market to continue to thrive, we need recurring revenues which come from the vehicle services and repairs we provide. The same holds true for these scan tool companies. They need to continue licensing new data, developing their tools to support new models, and come up with new innovative products that help us do our jobs more efficiently.
To support those initiatives, the tool company needs a revenue model that supports it. This is why the subscription model is popular. It’s sort of like becoming their business partner. You certainly want to see them succeed so that they can continue to develop and innovate. Just like your great customers want to see you continue to be there for them when they need you.
The future
Security is already becoming something that we’re getting exposed to and it will continue to provide challenges for us all. Now, I’m not talking about keys and key fobs. I’m talking about gaining access to certain modules or networks in the vehicle so we can conduct business. If you’ve come across a 2018+ FCA vehicle, you’ve likely encountered the “Secure Gateway” obstacle. This is a security measure implemented by FCA in order to protect critical systems such as driver assistance and telematics. In order to gain passage into the secure gateway, FCA has worked an arrangement with a third party called Integrity Security Services who runs a service called AutoAuth. According to AutoAuth’s website, they work with OEMs, Independent Tool Manufacturers, and Independent Service Providers in order to create a working security relationship with all parties. You can find more information at AutoAuth.com.
The National Automotive Service Task Force’s (NASTF) Secure Data Release Model (SDRM), is another security subscription worth looking into. One can obtain a Vehicle Security Professional (VSP) license by visiting NASTF.org. There’s definitely a process to get signed up, but one that can help you smooth out the challenges that lie ahead, especially when dealing with vehicles that contain what the OEM has classified as theft relevant parts or even reprogramming modules. In our shop, we’ve had to use our VSP in order to purchase transmission parts in the past. Without it, the dealer wouldn’t have sold us the parts.
We are operating in a complicated space as the automobile is one complicated machine. And for you, the service professional, the stakes are high and the motoring public is counting on you to be able to competently service and repair their vehicle. A lot has changed in the past forty years, but in the past ten years the technology curve has grown exponentially, and I don’t see it slowing down.
Training resources:
ETI - https://www.etools.org
Toyota - https://techinfo.toyota.com
NASTF - https://nastf.org
AutoAuth - https://autoauth.com
About the Author
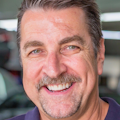
Scott Brown
Founder - Diagnostic Network
Scott is an ASE Master Certified Automobile Technician with L1, L3, & L4 credentials and has over 39 years of professional service industry experience. As an independent shop owner in Southern California and with his engagement at various levels of within our industry, he continuously strives to move the industry forward through networking, education, communications, and training. Scott is a founder of the Diagnostic Network (https://diag.net/) which was born in 2018 after he retired after 22 years at iATN, where he served as company president.
Brown is also the host of Professional Tool and Equipment News (PTEN) and VehicleServicePros.com podcast, Torque Factor. The podcast addresses the latest automotive service technologies while focusing on expanding knowledge and awareness around tools, equipment, education, and industry trends.