The conventional compression gauge was only designed to conduct a WOT cranking compression test. When using this gauge, I have always taught that the second compression stroke is the one that should be monitored. The reason being is that by the second compression stroke we can be assured that a full intake stroke would have occurred. There are cases whereas we could have good WOT cranking compression values and yet the engine may be suffering from a retarded valve timing issue or a wiped exhaust cam lobe. When using the electronic pressure transducer coupled to your original compression gauge hose and interfaced with a DSO, we can conduct four separate compression tests.
It is critical to keep the compression hose as short as possible. I believe that the maximum length should not exceed eight inches. This increases the accuracy of these four tests: WOT cranking, idle, cruise and WOT snap. Notice the compression versus RPM chart in Fig. 1. The idle, cruise and WOT snap tests are done dynamically with the engine running. When doing the tests, the Schrader valve needs to be removed from the compression gauge hose. See Fig. 2.
In Fig. 3, we are conducting a WOT cranking compression test with the Schrader valve still intact and the compression gauge hose on a two-valve engine. With each compression stroke the compression values increase. Notice the compression value of 130 psi on the second compression stroke. The second compression value is the one that should be monitored because we know that the piston would have conducted a full intake stroke.
Compression values are measured from the exhaust pocket at 0 psi and up.
Now let’s look at a high mileage 3.8L Chrysler in Fig.4, which shows a WOT cranking compression value of 125 psi. Fig. 5 shows an idle compression value of 45 psi. Next, Fig. 6 indicates a cruise compression value of 35 psi.
Finally notice in Fig. 7 that the WOT snap compression test matched the value that was captured during the WOT cranking compression test. If the WOT snap compression test showed a lower value than what was captured during cranking, we would suspect a retarded valve timing issue. The idle and cruise compression values are considerably lower than the value captured during the WOT cranking compression test because the engine is not pulling a lot of air with the throttle plates at an idle condition and barely open during the cruise compression test.
Now let’s take a look at a compression waveform and point out the critical points in Fig. 8.
All four strokes have occurred here between the two TDC events. The time between the two TDC events measures 100 milliseconds. If we divide 100 milliseconds by four strokes we know that a different stroke will appear every 25 milliseconds. The Pico brand DSO has internal software to identify all four strokes. Nevertheless, I prefer to do it the manual way. We have pointed out the exhaust valve opening and the intake valve opening. We may use the abbreviations of EVO for the exhaust valve opening and IVO for the intake valve opening in our scope captures. The point of the exhaust valve opening and the point of the intake valve opening can be monitored to diagnose a retarded valve timing issue or a wiped cam lobe, as well as a restricted exhaust as you will see in this article.
On the high mileage 3.8L Chrysler engine, we captured two TDC events. We now know that the crank has turned 720 degrees. In Fig. 9 notice that the time between the 2 TDC events measures 176 milliseconds. We divide this time by four to represent the four strokes. This means that every 44 milliseconds will represent a different stroke. If we move the first cursor over to the 44-millisecond mark, we just identified the exhaust stroke, or BDC, or 180 degrees. See Fig.10. Notice that the 180-degree cursor pretty much split the exhaust ramp in the middle.
Fig. 11 shows where the 180-degree cursor should split the exhaust ramp. Notice on the right of Fig. 11 you can see where the intake ramp should be in relationship to the 360-degree cursor. Fig 12 is where we moved the 360-degree cursor to the 88 millisecond mark which identifies TDC of the intake stroke. This would only apply to engines with fixed valve timing. If the cam timing is off one tooth, the cam timing will be retarded 13 degrees. You may also notice that channel two is indicating the firing event from this cylinder. Notice that the firing event occurred before TDC of the compression stroke. This verifies good spark timing.
Remember that the WOT snap compression values should match that of the value obtained during WOT cranking. On engines equipped with electronic throttle control, a snap test will not give us 100% throttle opening. The snap test at the accelerator will give us about 40% throttle opening on engines equipped with electronic throttle control, which is a sufficient enough gulp of air that should match what was captured during the WOT cranking compression test. We stated earlier that if the Snap compression test was lower than the WOT cranking compression test, we would suspect a retarded valve timing issue. When performing these tests, it is critical to use a compression gauge that has a maximum length of eight inches. If your compression gauge hose is longer than eight inches your measurements will not be accurate. Fig. 13 shows the valve timing specs for this 3.8L Chrysler engine. Most domestic engines equipped with fixed valve timing will be very close to these specs. You can see in our compression waveforms the valve timing is very close to these specs.
On overhead cam engines, valve timing issues are more common compared to the conventional cam-in-block pushrod engine. You may have an engine such as a SOHC (single overhead cam) engine where we would have to monitor the EVO point on both banks if we suspect a retarded valve timing issue. On engines such as DOHC (double overhead cam) engines we would need to monitor the EVO point and the IVO points on both cams on both banks.
Modern day engines that are equipped with variable valve timing control systems will usually have robust cam timing parameters available via scan data, but you will see that this parameter is unstable as the RPM changes. In the event of wiped cam lobes, we can detect that very easily by viewing the compression waveform. We will show this problem later in this article.
Let’s take a look at a domestic DOHC engine to see what the cam profile looks like. The domestic engines that are equipped with variable cam timing will retard the exhaust valve timing off idle and advance the intake cam timing off idle. This creates valve overlap which increases the engine’s ability to breathe at higher RPMs. This also eliminates the need for EGR systems. During off idle on these engines, the intake valve opening is advanced and the exhaust valve timing is retarded. This allows the engine to pull in some inert exhaust gases which eliminates the need for an EGR system. At an idle condition with a 0% duty cycle command to the VVT control solenoid, the cams will go back to their default condition. The exhaust valve timing goes back to an advanced position while the intake cam timing goes back to a retarded position. Engines imported from Asia do the exact opposite, which allows valve overlap at off idle conditions.
In Fig. 14 on a domestic DOHC engine equipped with VVT, notice the time between the two TDC events measures 209 milliseconds. We divide this value by four and can determine that each stroke will occur every 52 milliseconds. Fig. 15 is where we placed the second cursor at the 52-millisecond mark which now identifies BDC or the 180-degree mark. You can see that there are 10 minor divisions between the TDC event and the 180-degree cursor. This tells us that the crank turned 18 degrees per each minor division. Notice that the EVO point is advanced and occurred three minor divisions before the 180-degree cursor. Three multiplied by 18 tells us the exhaust cam is advanced 54 degrees at idle. This is a default value captured at idle. Now let’s take a look at the IVO point captured at an idle default position in Fig. 16. Notice that we moved the second cursor to the 104-millisecond mark which identifies the 360-degree TDC mark.
We know that the crank turned 18 degrees per minor division. Notice that the IVO point is retarded and occurred three minor divisions, or 54 degrees, after TDC. Again, these values were captured at idle where the cams come back to their default positions. The domestic engines will retard the exhaust cam timing off idle and advance the intake cam timing off idle.
Now let’s look at some problem vehicles. In Fig.17 notice there appears to be two compression strokes. Notice that the second stroke is considerably lower than the first. This waveform was captured from an engine with a broken exhaust valve rocker arm. Since the exhaust valve didn’t open, the exhaust pressure came back through the intake valve on the next intake stroke. We talked earlier that when viewing a compression waveform, we can easily pinpoint a wiped cam lobe which seems to be a common problem on modern day engines. Look closely at the exhaust ramp in Fig. 18. You can easily suspect that the EVO point occurred later. In addition, notice the increase of exhaust pressure at the end of the exhaust ramp. This tells us the exhaust valve opened later and closed earlier from a wiped exhaust cam lobe.
This next example comes from a call from another shop. More often than not, technicians overlook the basics. A high mileage 3.4L engine had a dead miss. Fig. 19 shows a low WOT snap compression value of 66 psi. It would be easy to condemn this engine and recommend the owner pull the plug on this vehicle. Let’s go ahead and look at the compression waveform at idle in Fig. 20.
We are triggering from channel two at the plug wire. Did you notice the firing event occurred on the exhaust stroke? Further examination found that two secondary leads were crossed. The low WOT snap compression values were low due to cylinder being washed down with raw fuel which reduces the cylinder sealing ability. This problem occurred after the car owner replaced the coils, secondary leads and spark plugs.
Fig. 21 was captured from an engine suffering from a lack of power complaint. Notice that during the exhaust stroke captured during an idle condition the exhaust pressure is increasing. This was due to a restricted converter. You need to be careful here because a wiped exhaust cam lobe could create the same waveform. However, we previously covered what a wiped cam lobe would look like. Let’s look at a compression waveform captured during a WOT snap test in Fig. 22. Notice the exhaust pressure peaked at 19 psi from a restricted converter.
Retarded valve timing issues are becoming more common on today’s modern engines. We previously discussed focusing on the EVO point to pinpoint a retarded valve timing issue. In Fig. 23 let’s focus on the IVO point to determine if we have a retarded valve timing issue. Notice the IVO point occurred after the 360-degree cursor. We established earlier that the crank turned 18 degrees per minor division. Notice that there are three minor divisions between the IVO point and the 360-degree cursor. The valve timing is off 54 degrees. If you refer back to Fig. 11 you can see that the IVO point indicates a retarded valve timing issue.
Testing the engine’s mechanical integrity through the spark plug hole with a pressure transducer will yield a lot of information, and it’s proven to be much easier than an engine tear down.
The industry is better because of your commitment.
About the Author
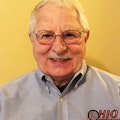