The Ins and Outs of Working on Automatic High Beams
As a driver, I have certainly experienced an oncoming vehicle that has its high beams on, and the blinding glare that you get as the vehicle approaches and passes. With today’s brighter headlight assemblies, this can be more than a distraction, and taking your eyes off the road isn’t the safest scenario.
When asked most drivers will tell you that they use their high beams on country and back roads or when there are few if any street lights. But research has shown that the high beams often go unused when driving at night, even though they would enable the driver to see more clearly.
There are explanations for this. Drivers generally think the road in front of them is lit well enough with just the low beams, especially on highways and roads that are equipped with streetlights. Another major factor is that they are worried about distracting other drivers with the glare of their high beam lights. It is these situations that have led manufacturers to equip their vehicles with automatic high beam systems, increasing nighttime visibility and possibly reducing nighttime accidents.
Automatic high beam systems are a common safety feature on today’s vehicles, and the system is usually bundled in a safety options package with a clever unique name. Toyota calls its system the “Toyota Safety Sense.” Honda calls its system “Honda Sensing.” GM has “IntelliBeam,” and Ford incorporates the system in its “Ford Co-Pilot360.” Vehicle safety is important to today’s automotive manufacturers, and that is one reason many have chosen to equip their vehicles with an automatic high beam system.
So how does this technology work and what can we expect to see as these vehicles start showing up in our shops for service?
The main component required in an automatic high beam system is a forward-facing camera that is able to recognize the lights of an oncoming vehicle or the rear lights of a preceding vehicle. The addition of an automatic high beam system to an existing vehicle’s infrastructure may not require any extra components, possibly just added software for functionality. Forward-facing cameras are quite standard now, and yaw sensors that are used in stability control and airbag systems have been on vehicles for a long time. Several vehicle manufacturers use the yaw sensors data as an input for regulating automatic high beam operation.
The forward-facing camera responsible for automatic high beam function must have the ability to analyze the light that it detects for intensity, color and movement. These cameras are able to detect the lights of an approaching vehicle from a distance of greater than a quarter-mile on a flat and straight road. When the camera detects these lights and the system is operational, the software in the module that manages the automatic high beam operation will then decide what to do. It will either turn on the high beams for better visibility or turn them off, returning to low beam operation to prevent glare. Because the system relies heavily on the use of the forward-facing camera, anything that could block the camera’s view might affect its operation. Snow, ice and dirt on the windshield can affect the camera’s ability to see properly, as can vehicle road spray, fog, heavy rain, smoke, dust or other airborne conditions.
The forward-facing camera is usually mounted near the top of the windshield, close to the center of the vehicle, or it may be integrated into the rearview mirror assembly.
For the automatic high beam system to function, certain operational and environmental criteria must be met. Each manufacturer will have their own way of doing things, and their own names that they give to the modules that are controlling the system’s function. But almost all of today’s systems will have the following characteristics that will need to be met for the system to become operational, functional and active.
To enable automatic high beams to turn on and function:
The system must be activated, commonly through the driver information center or driver features screen/menu or the headlight switch.
The headlight switch must be in the correct position, auto high beam typically.
The vehicle speed is above a set minimum, this varies and is manufacturer-specific, but the range is 12 to 45 mph. Vehicle speed is used to prevent excessive toggling of the high beams.
Ambient light conditions are dark enough. This is usually decided by the ambient light sensor on the dash used by the HVAC for sun load detection.
The forward-facing camera doesn’t detect any light sources that it decides are head or tail lights.
The automatic high beams will turn off and return to low beams:
- If the forward-facing camera and the accompanying software detect a light source from a vehicle that it decides is either a headlight or taillight.
- The ambient light isn’t dark enough.
- The vehicle speed falls below a set minimum speed for a predetermined length of time. This is manufacturer specific, but the range is 12 to 27 mph.
- The auto high beam switch is turned off.
- The forward-facing camera decides that its vision is impaired or blocked.
These are the most common activating and deactivating criteria that will allow the automatic high beam system to function. But when we are diagnosing or investigating an operational complaint, it is important to look up the specific make and model that we are dealing with using our information system to verify proper operation. And don’t forget that the vehicle’s owner’s manual is a valuable source of operational and function data.
On a 2017 GMC Sierra, for example, there is not an option in the drivers settings menu to enable the automatic high beam system, but there is an “auto” setting on the headlight switch. To enable the automatic mode on this truck, you need to move the high beam lever from the low beam position to the high beam position twice within two seconds, this will activate the system. When the system is activated, the green automatic high beam assist light will be illuminated on the dash instrument cluster, indicating the system is functional. This system will be disabled from automatic mode if the driver moves the high beam lever forward from the low beam position to the high beam position or a flash-to-pass operation. It will then need to be reenabled to restore automatic mode. It also won’t allow automatic mode if the fog lights are turned on. The 2017 GMC Sierra’s forward-facing camera requires a scan tool, but no targets to perform recalibration if the windshield or camera are removed or replaced. But if the front-facing camera is replaced, it must be reflashed and programmed before it will allow calibration or relearning.
There is a technical service bulletin (TSB) related to the IntelliBeam system on the 2015-2020 GMC pickups and other IntelliBeam equipped vehicles. TSB #PIT5535E states that diagnostic trouble code (DTC) B1008:4B (Front View Camera Module Calibration) might be set if the forward-facing camera is not properly mounted or something is obstructing its view. The TSB instructs us to ensure that the camera is fully seated in its mounting bracket and that there is nothing blocking its view. This TSB also points out that a substandard windshield or an improperly installed windshield may result in an excessive top gap between the windshield and roof. The specification on that gap is 0.14 to 0.18 inches. If the gap is excessive, it might not allow the forward-facing camera to be correctly installed and cause wind and water leaks.
The 2018 Honda Odyssey requires a forward speed of 45 mph to activate the automatic high beam system, much faster than other manufacturers. It will also deactivate the system if the vehicle senses that it is being driven on a winding road or up and down steep hills. It does this by using the yaw sensors in the vehicle stability and airbag modules. Honda does supply DTCs and diagnostic data to aid in diagnostics. If the windshield or the forward-facing camera is replaced on this Odyssey van, the system will need to be recalibrated using a scan tool and targets to ensure proper and safe operation.
The 2017 Toyota Camry automatic high beam system will supply system data and diagnostic trouble codes, and it also incorporates data from the yaw sensor for functionality. If there is a failure in the Toyota automatic high beam system, the “Check Auto High Beam System” message will be displayed on the driver’s information center and manual high beam operation will result. The Camry’s forward-facing camera requires recalibration if it is removed, replaced or the windshield is replaced. To perform this recalibration, a scanner and special targets will be needed.
2019 Ram trucks can be fitted with an Auto High Beam Control (AHBC) option. The Ram AHBC comes in two configurations: either a Combined Rear View Mirror Module (CRVMM) or a Driver Assistance System Module (DASM). The DASM is what Ram calls its forward-facing camera. The AHBC must be enabled on the Ram truck in the radio display or the Uconnect system settings under the “Auto Dim High Beams.” If the DASM on a Ram truck is removed for service or is removed during a windshield replacement, there is a special installation procedure that must be followed. If the proper procedure isn’t followed a C008F-00 Calibration not learned DTC or C14A4-00 Sensor Adjustment Required DTC could be set. The use of a digital inclinometer (a common cell phone app) is needed to aim the DASM and then the procedure is completed by following the instructions on the scan tool under the heading “DASM Auto Alignment.”
If there is an issue in any of the connected systems of the automatic high beams, the system will shut off, and manual high beam operation will be enabled. There may or may not be a warning symbol to indicate to the driver that there has been a failure in the system, again this is manufacturer specific. Diagnosing and repairing an automatic high beam system will almost certainly require a scan tool, a good information system and possibly the use of special equipment.
But even a simple repair such as a battery replacement may disable the automatic high beam system because this system could rely on the vehicle’s yaw sensor for proper operation. And a battery disconnect may require the yaw sensor to be recalibrated. The forward-facing camera may need to be recalibrated if removed or if a windshield is replaced. Verifying that you are capable of performing these procedures before you commit to diagnosing or replacing components is important. The automatic high beam system may seem like a simple add-on safety device, but with all the systems on today’s vehicles being so heavily interconnected, it’s a straightforward yet complicated protection system.
Jeff Taylor boasts a 30-plus-year career in the automotive industry as a fully licensed professional lead technician. Jeff works for the CARS Training Network Inc. in Oshawa, Ontario, Canada. He is also heavily involved in government focus groups, serves as an accomplished technical writer, and he has competed in international diagnostic competitions as well as providing his expertise as an automotive technical instructor for a major aftermarket parts retailer.
About the Author
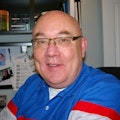
Jeff Taylor
Jeff Taylor is a seasoned professional at CARS Inc. in Oshawa with 40 years in the automotive industry. As a skilled technical writer and training developer, he holds licenses in both automotive and heavy-duty vehicle repair. Jeff excels in TAC support, technical training, troubleshooting, and shaping the future of automotive expertise.