The process of supplying air to the internal combustion engine’s cylinders is called aspiration, and it involves the induction or intake system of the engine. Engine aspiration takes two forms: naturally aspirated (NA) or forced induction. The NA engine is relying only on atmospheric pressure to fill its cylinders with fresh air. When the NA engine’s pistons travel down during their intake strokes, they create a partial vacuum, and atmospheric pressure will push the air into that void.
The forced induction engine will use some form of mechanical means to force more air into the cylinders than atmospheric pressure will provide, and that extra air mass will increase the effective engine compression ratio. The forced induction system will use either turbocharging or supercharging to push or force more air into the cylinders than atmospheric pressure alone will supply. This raises the pressure of the induction system above atmospheric pressure, resulting in better fuel economy (under normal operation) and increased engine power output.
The forced induction system achieves these improvements by forcing the same amount of air into a small displacement engine that a large NA displacement engine would normally consume. This is one reason the manufacturers are leaning heavily on the forced induction system on today’s models even when they are hybrid equipped models.
This does not mean that the NA engine is going away anytime soon. Improvements in the NA induction system have advanced the efficiency of this type of induction, and they are continuing.
Plastic Intake Manifold
The use of a plastic intake manifold is now the norm on both the naturally aspirated and turbocharged engine. The plastic intake manifold is used to evenly distribute the intake air via equal length runners to each intake port on the engine’s cylinder head.
Plastic intakes are cheaper to manufacture and lighter than the older metal intake design. The plastic intake manifold slows the transfer of the engine’s heat to the intake air, allowing the intake to supply a cooler, denser (more powerful) air mass to each of the engine’s cylinders. A distinct advantage is the smooth uniform interior surface of intake runners which delivers a less turbulent airflow to each cylinder and that translates to more power. Engine power, torque and fuel efficiency can be improved by using variable length intake manifold runners, air tumbling features or by varying the size or dimensions of the intake plenum. These features are easily achieved during the molding process and accomplished using the plastic intake manifold all while maintaining the required engine packaging size. But these increases in power and efficiency do come at a cost. Plastic intakes tend to be noisier, and some earlier designs lacked the strength and durability of their metal predecessors, but most of these issues have been addressed.
Turbocharger Designs
The turbocharger is the most commonly used form of forced induction found on today’s vehicles. The use of a turbocharger on a small displacement engine, for example, a 2.0L 4-cylinder engine can create the same power output as a 3.0L V6 engine with 20-40% better fuel economy.
There are two common turbocharger designs used today: the single-scroll or the twin-scroll. The typical turbocharger will provide a boost pressure of between 6 and 8 psi.
The turbocharger’s turbine is propelled by the hot exhaust gas flow (thermal energy), that drives the compressor, forcing more air into the induction system. The turbocharger is not mechanically driven by the engine, so the increase in power and engine efficiency is provided without adding extra mechanical strain to the engine.
A downside of the turbocharging system is turbo lag. This lag is created by the delay time (about one second) it takes for the engine to create enough exhaust pressure to spin or “spool up” the turbocharger turbine. Turbo lag is most noticeable at low speeds and low RPMs.
Manufacturers are looking for a linear power delivery from their engines and do not want customers to experience turbo lag.
Complex, three-dimensional, spiral-shaped turbocharger compressor wheels have been designed, optimizing induction air speed, pressure and temperature all while limiting turbulence formation. Turbulent airflow in the compressor area of the turbocharger will reduce efficiency and exaggerate turbo lag. Manufacturers have favored the use of a smaller turbocharger or multiple small units on V6 / V8 engines to lessen the turbo lag affect. Smaller turbochargers employ a small lightweight compressor wheel, with less inertia, which will spool up faster, reducing lag.
The single-scroll turbocharger with its single exhaust turbine inlet can in some cases allow cylinder exhaust pulses to interfere with each other, limiting its efficiency and exaggerating turbo lag.
Using the twin-scroll turbocharger design (effectively two small turbochargers in one housing) all but eliminates turbo lag by using two separate exhaust gas flow turbine inlets. The twin-scroll design separates the exhaust cylinder pulses that interfere with each other reducing turbocharger and engine efficiency.
Examining the exhaust stroke cycles of the common 4-cylinder engine with a 1-3-4-2 firing order, when No. 1 cylinder is ending its power stroke and just opening its exhaust valves, No. 2 cylinder’s exhaust valves are still open (valve overlap). On a single-scroll turbocharger equipped 4-cylinder, the exhaust gas pressure pulse from No. 1 cylinder is going to affect No. 2 cylinder’s ability to expel its exhaust gases, due to exhaust reversion. Exhaust reversion is the flow of exhaust gases back into the cylinder.
The twin-scroll turbocharger design reduces this exhaust reversion issue by pairing mating cylinders No. 1 with No. 4 to one individual turbocharger turbine inlet and cylinders No. 2 with No. 3 to a separate distinct turbocharger turbine inlet.
It’s important to note the twin-scroll turbocharger is employed on some inline 6-cylinder engines, again pairing the mating cylinders into common turbine inlets. BMW does this on their 6-cylinder engines. BMW refers to their twin-scroll turbocharger equipped engine as the “BMW TwinPower Turbo.”
When combined with a specifically designed intake manifold and active valve train control, the twin-scroll turbocharger provides more effective exhaust gas scavenging, allows for greater engine valve overlap, improves turbocharger efficiency, and provides better low-end response over the single-scroll design, while still delivering high output power.
The variable-geometry turbocharger (VGT) design is also used to lessen the turbo lag effect. The VGT will control the amount of exhaust gases that flow onto the exhaust turbine. By doing this you have the best of both worlds; a large blade turbocharger that performs well at high RPMs and a small blade turbocharger that works well at low-mid RPMs (the most common driving range).
Supercharger Options
The supercharger is a positive displacement air pump that will deliver a fixed volume of air per supercharger revolution, increasing the pressure of the induction system. The supercharger boosts engine horsepower and torque by increasing the air mass being forced into the engine cylinders. The supercharger is directly driven by the engine, often by a drive belt and this direct link to the engine creates an instantaneous power boost without any lag.
Supercharging is often used on large displacement engines because it will create significantly more power than a turbocharger. Superchargers used by the OEMs typically boost the induction pressure by 5 to 15 psi. Superchargers deliver a smooth linear power boost from low to high engine RPMs. But this linear power boost does come at a cost, as the supercharger creates a parasitic drag on the engine, slightly lowering fuel economy (particularly in high-performance applications) and they are often noisier than a turbocharged engine.
There are three common supercharger designs being used today:
The Roots supercharger uses a set of triple-lobe 60-degree twisted helix rotors that will compress the incoming air to a positive pressure against the outside walls of the assembly as they rotate. This is the most popular but least efficient supercharger design.
The Twin-Screw supercharger (or Lysholm Twin-Screw Supercharger, named after the inventor) uses a set of meshing, twisting conical shaped tapered rotors, which will squeeze the air pockets between the rotors as they rotate. This type of supercharger is more efficient than the Roots type but is more expensive to manufacture.
The Centrifugal supercharger uses an engine driven impeller spinning at 50-65,000 RPM to pressurize the intake air. This style of supercharger is the smallest, lightest and most efficient, but most exotic type. It looks like a turbocharger and is used on the Koenigsegg super car. It works best at very high engine RPMs.
The intake manifold of the supercharger-equipped engine still favors the cast aluminum design, especially for the lower section because it often contains the integrated supercharger assembly and the intercooler. Typically, the upper cover is now plastic, but aluminum is often still used for strength and noise suppression.
Both the turbocharger and the supercharger are going to increase the temperature of the intake air stream because they are compressing it. For both of these forced induction systems to work at peak efficiency, the heat of that compression needs to be removed. Hot intake air is less dense and cannot supply the same amount of power as cooler air.
The Intercooler
An intercooler is used to remove this heat and increase the density of the air before it enters the engine via the intake manifold.
There are two basic intercooler designs: air-to-air and air-to-water. These are often integrated into the intake manifold of the engine. Many of the air-to-water intercooler systems use the engine’s cooling system to remove the heat from the compressed air, transferring it to the cooling system so that it can be removed by the radiator. Other air-to-water intercooler systems, like the 2021 Ford 5.2L SC Mustang, have their own dedicated cooling system, coolant pump and radiator. The air-to-air intercooler design often associated with a turbocharged engine will route the hot compressed air to the grill area where the intercooler will be mounted shedding the heat to the atmosphere.
Neither the NA nor forced induction system have escaped issues. The early plastic intake manifolds were prone to cracking, breakage, EGR heat damage and coolant corrosion. Rubber throttle body boots/snorkels decomposed because of oil contamination or the constant flexing and engine vibrations causing induction leaks. Vacuum leaks are still a common issue on the NA induction system and will turn on warning lights and set diagnostic trouble codes. Turbocharged systems suffer from the loss of boost pressure, triggering warning lights, affecting drivability, and often creating noise or whistling complaints caused by leaks from the induction system. Turbocharger issues are common, for assorted reasons...wastegate failures, control issues, ignoring service intervals, and use of improper engine oil are all common causes of turbocharger failure. Supercharger gear whining and drive clutch noises are common. The forward mounted air-to-air intercoolers suffer road debris and corrosion issues that can cause leaks.
The induction system of today’s vehicles is a vital component in the overall engine management system. The trend is away from the NA engine for reasons of efficiency and power output and toward the forced induction engine. The use of the current forced induction technology has increased engine power output while reducing the engine’s displacement size, all while still meeting the common goal of reducing exhaust emissions and increasing fuel economy.
About the Author
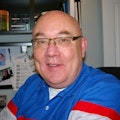
Jeff Taylor
Jeff Taylor is a seasoned professional at CARS Inc. in Oshawa with 40 years in the automotive industry. As a skilled technical writer and training developer, he holds licenses in both automotive and heavy-duty vehicle repair. Jeff excels in TAC support, technical training, troubleshooting, and shaping the future of automotive expertise.