With the widespread use of Electric Power Steering (EPS) systems in recent years, the automotive industry has undergone a substantial upheaval. These systems provide better fuel efficiency, improved driving, increased reliability, and have almost completely replaced the conventional hydraulic power steering systems on most vehicles.
The belt-driven hydraulic pump reduced fuel economy, because it worked continuously and consumed engine power even when steering assistance wasn't needed. It also needed regular maintenance, had parts that quickly wore out, and was prone to fluid leaks. The EPS system is more efficient and compact, getting rid of the hydraulic pump, hoses and fluid reservoir.
Although effective, the early EPS systems lacked the road feel and sophistication of the more recent EPS systems. Today’s EPS is tightly integrated with innovative driver-assistance features all while providing great road feel for the driver.
Both the driving experience and safety of these EPS-equipped vehicles were improved by these and other advances. Automakers eventually focused on the advantages of EPS and started implementing them into a larger selection of their vehicles. Another factor leading to the implementation of EPS was that hybrid vehicles don’t always have a running engine, and electric vehicles don’t have an engine at all to drive the hydraulic power steering pump. A substantial part of today's fleet is either hybrid or fully electric, so the EPS system has been embraced. But there are benefits and advantages to employing EPS on conventional Internal Combustion Engine (ICE) vehicles as well.
- Energy Efficiency: EPS systems are more energy-efficient compared to traditional hydraulic power steering systems because they only consume power when steering assistance is needed. In hybrids and EVs, where energy conservation is crucial for maximizing range and efficiency, EPS contributes to energy savings.
- Regenerative Braking Integration: Hybrids and EVs use regenerative braking systems to recover energy during deceleration for effective efficiency. The EPS systems can be integrated with regenerative braking, enhancing the overall energy recovery process. During the regenerative braking phase of a hybrid or electric vehicle, the side-to-side regenerative brake distribution can become imbalanced due to a turning maneuver, uneven road surface or other factors. This can cause a pull or lead feeling through the steering to the driver. If the vehicle is equipped only with a rear electric drive motor, dual electric motors or a hybrid front and electric rear motor, the regenerative braking torque can apply to only one axle. This could cause a braking imbalance from front to rear. This situation can have a considerable impact on vehicle handling and stability when cornering or braking. Today’s hybrid and electric EPS systems will take regenerative braking into consideration to counteract the issues that regenerative braking forces can cause, while still maximizing energy harvesting efficiency and keeping the vehicle stable and safe.
- Weight Reduction: EPS systems are generally lighter than hydraulic power steering systems because they do not require a hydraulic pump, fluid reservoir or associated components. The reduced weight contributes to improved vehicle efficiency and handling.
- Variable Assistance and Variable Ratio: EPS systems can supply variable assistance based on driving conditions. At lower speeds or during parking maneuvers, EPS can supply maximum assistance, making steering effortless. At higher speeds, it can reduce assistance to improve stability and energy efficiency. Some EPS designs will allow for variable turning radius and a decreased turning radius in certain conditions, such as a parking maneuver.
- Integration with Vehicle Control Systems: EPS systems can be tightly integrated with other vehicle control systems, such as stability control, lane-keeping assist, automatic parking and many other automated driving features.
- Quiet Operation: On electric vehicles, where noise levels are often lower than in conventional ICE vehicles, EPS systems run silently, which is noticeable. This makes driving quieter and enjoyable as a result.
- Maintenance and Reliability: EPS systems generally require little maintenance compared to hydraulic power steering systems. This can result in cost savings and increased reliability for hybrid, EV and ICE vehicle owners. Steering Feel Adjustment: The EPS systems allow for continuous and variable adjustment of steering feel. Often the EPS system allows the driver to adjust the steering feel via dash or other driver control adjustments. This feature can be used to tailor the driving experience to the driver's preferences, enhancing comfort and drivability.
Operation and Components
The EPS system features an Electronic Control Unit (ECU). The EPS ECU receives and processes the steering angle data, torque sensor data and many other pieces of data from modules across the vehicle platform. This data is shared and supplied via the vehicle’s high-speed communications network (CAN). This shared data can include but is not limited to; vehicle speed, stability and braking module data, forward facing camera data, parking sensor data and many other bits of information. All this information will allow the EPS ECU to decide how much steering is necessary, and in what direction.
EPS operation is started by the driver turning the steering wheel. Sensors measure the amount and rate of steering wheel movement when the driver rotates the wheel. A torque sensor (there can be multiple) and a steering angle sensor are mounted in the steering column or the steering rack. The torque sensor measures the amount of force being applied to the wheel, as opposed to the steering angle sensor, which tracks the steering wheel's position. To calculate the proper amount of power steering needed, the EPS control module considers the input from the torque sensor together with other vehicle factors such as vehicle speed. The EPS system will offer extra steering power if the torque sensor notices that the driver has supplied a sizable amount of torque, showing a desire for more steering effort. On the other hand, if there is little torque being applied to the steering wheel, the system might supply less steering power to enhance the road's sensation. The torque sensor is a critical sensor in the EPS operation and there are variations being used. Strain gauge, Hall effect and optical torque sensors are all being used. Each is functionally different and will require specific diagnostics if they fail, but they perform the same job: they are reporting the amount of driver input (torque) being applied to the steering wheel.
Typically, the torque sensor is integrated into the steering rack assembly and can’t be changed or serviced. But if a service (alignment) or a replacement part is installed, following the repair instructions carefully and proper calibration must be performed using a scan tool to ensure a safe and functional EPS system.
When the EPS ECU decides that steering is necessary, based on the driver's steering input or another of the vehicle's operational conditions, the ECU will send signals to activate a high-power electric motor that will generate the needed torque to perform the steering operation.
This electric motor can be attached to the steering rack using various arrangements. The rack assist design is the most popular and can be a belt drive, dual pinion or single pinion design. But the column assist design, with the motor attached to the steering column, is also used.
To improve the comfort and control of the driver, EPS systems can supply feedback to the driver that will replicate how the road feels by adding some resistance to the steering wheel. The EPS can even alert the driver to pay attention to conditions by putting a haptic response into the steering wheel to alert the driver. Additionally, to help stabilize the vehicle, EPS systems often cooperate with other safety elements like stability control systems and ABS braking. This combination of EPS and other systems can be used to correct trailer swaying conditions on an EPS-equipped towing vehicle. The EPS can even lighten the driver's fatigue levels by neutralizing a strong crosswind when driving by applying a slight lead with the EPS to counter the crosswind.
All EPS systems today are built with a fail-safe mode that enables manual steering in the event of a system failure or power loss. (They are not driven by wire yet). This guarantees that if an EPS failure occurs, the vehicle can still be securely steered.
EPS Issues
One of the most obvious indicators of an EPS issue is a difficult-to-turn steering wheel. But the EPS is a safety system, and the EPS ECU will be constantly performing diagnostic tests on itself to ensure the system is fully functioning. If an issue is discovered during this self-testing, the EPS dashboard warning light will be illuminated and the system may shut off completely or go into a default, limited or reduced power assist mode.
When in reduced power assistance mode, there will be limited power steering assistance until the issue can be repaired or the issue resolves itself. Holding the steering wheel to full lock on an EPS system could overheat the high-power motor performing the steering movement and put the EPS system into reduced power assist mode until the motor cools off. This is important to know when diagnosing an issue that can’t be duplicated. In such cases, consider if the issue customer created.
Unusual noises are another sign of possible EPS issues. Unusual steering noises like grinding, whining or clicking sounds could be the consequence of problems with the EPS system's electric motor, gears or other parts. (A seized lower steering u-joint can easily be misdiagnosed as a code setting EPS issue.)
Diagnosing Electric Power Steering Issues
Visual inspection, digital diagnostics using scan tools, an oscilloscope or DVOM are commonly used to diagnose EPS concerns.
Begin by visually inspecting the EPS components, including the electric motor, wiring and connectors. Look for any obvious signs of damage, loose connections or corrosion. Diagnosing the problem and repairing the problem are going to involve a scan tool. Scan the system for Diagnostic Trouble Codes (DTCs). These codes can provide valuable information about the problem. Common EPS-related trouble codes include C1513 (Torque Sensor Zero Point Adjustment Incomplete), C1514 (Torque Sensor Malfunction), C1560 (Motor Malfunction) and others. 2011-2016 Ford Explorers can set a P07AE (a transmission-related powertrain control code) for excessive effort to turn the wheels. The code often sets immediately after the EPS stops working. If the visual inspection does not show a seized lower ball joint, tie rod, upper strut mounts or stuck steering u-joints, the issue could be the steering rack binding internally. But be aware that this P07AE code could also set for low tire pressures, so inspecting the entire system is imperative.
Another common Ford DTC is U0131, set in the ABS unit and there will be no communication with the EPS ECU. Evaluating the Ford EPS system is straightforward. The wiring has only five wires: a 100A power feed, ignition on voltage, ground and HS CAN+ and HS CAN-. We will be checking for good power and grounds using a load to ensure the circuits are good, and then we will be looking at the communications line to ensure we have CAN activity on the lines. We can scope the CAN line. Often the small ignition feed wire going to the Power Steering Control Module (PSCM) will be damaged by the protective insulating sleeve near the exhaust. If all the wiring tests are OK, and there is still no communication with the PSCM, we are likely dealing with a failed PSCM.
Post repairs of an EPS system typically require the scan tool to calibrate, reset, reprogram (many EPS units incorporate the ECU Module) or initialize the system. Following the proper manufacturer's specific instructions will ensure the EPS system will function as it was designed to.
The evolution and widespread adoption of electric power steering systems in today's vehicles have revolutionized the automotive industry. These systems offer numerous advantages, including improved fuel efficiency, enhanced driver control and reduced maintenance requirements. However, diagnosing and repairing EPS system issues can be more complex than traditional hydraulic systems due to their electrical and sensor-based nature. Despite a few recalls related to safety concerns, EPS systems continue to play a vital role in making vehicles more efficient, and making them safer for drivers and passengers alike. As technology continues to advance, we can expect further improvements and refinements in EPS systems, contributing to the future of automotive innovation.
About the Author
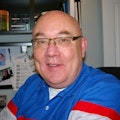
Jeff Taylor
Jeff Taylor is a seasoned professional at CARS Inc. in Oshawa with 40 years in the automotive industry. As a skilled technical writer and training developer, he holds licenses in both automotive and heavy-duty vehicle repair. Jeff excels in TAC support, technical training, troubleshooting, and shaping the future of automotive expertise.