Scan data diagnostics began on the GM systems in the early ‘80s. The Chrysler models began giving us scan tool data and functions in the mid-‘80s. In comparison I have always felt the Chrysler system proved to be very robust.
The Chrysler computer system began with a two-wire system known as CCD. The DLC connector uses two circuits to communicate with the scan tool known as Receive and Transmit for PCM and TCM data. The point here is that there will be no communication with the scan tool until a request is made by the scan tool. The Receive and Transmit circuits are dedicated to engine and transmission data only. On the early CCD systems, the other modules communicated on the CCD+ and CCD- circuits. In the early ‘90s the CCD systems were being phased out and a single wire PCI circuit was introduced. The PCI buss circuit reports data to pin 2 of the DLC. The same rule applies in that the PCM and the TCM will communicate on a two-wire Transmit and Receive circuit. The same rule applies in that a request must be made by the scan tool before the PCM or the TCM sends data. The single wire PCI bus is used on all the other modules. When Chrysler went fully CAN compliant in 2008 the PCM and the TCM communicated on a two-wire CAN High & CAN Low circuit.
Pin 6 of the DLC is known as CAN High while pin 14 is known as CAN Low. On Chrysler CAN compliant systems there is no activity on the bus circuit until a scan tool is connected and a request is made.
Though the bus circuits have changed since the mid-‘80s, the scan tool data and functions have been uniform and more robust as the years changed. The framework of thIs article will cover the data and functional tests from the PCM platform. We will focus on the modern-day systems whereas Chrysler introduced a new PCM known as NGC or Next Generation Controller. There are two versions, one being the Huntsville Controller, and the second being the Motorola controller. The Huntsville controller can be identified by its cooling fins See Fig.1. These controllers are not interchangeable, nor can they be flashed from another VIN vehicle. However, one aftermarket scan tool company has found a way to write a new VIN to a salvage yard PCM. The results of this vary from a successful process to a failure so it is not reliable to pursue this strategy.
Access to the bus circuits has undergone a major change from the folks at Chrysler beginning in MY 2018. Access on the global side of the scan tool is easy and automatic. However, due to the considerable number of cyberattacks on these vehicles, Chrysler has enlisted a server that the user of a scan tool must connect to before accessing the enhance side of the PCM with the scan tool. See Fig. 2 The reason for this: should a cyberattack occur and the vehicle is stolen, the website would have a record of who accessed the theft deterrent system. Put simply, you will need to be online with your scan tool to access the enhanced side of the scan tool. There is another option that is not a good choice which involves buying a Y adaptor cable that interfaces the scan tool to the security gateway module. See Fig. 3. The problem here is that access to the security gateway module is very difficult. Most of these modules are located deep inside the dash behind the radio or HVAC control panel. Whenever accessing the bus circuits on Chrysler systems, Chrysler uses its same old strategy in that there will be no activity on the bus circuits unless a scan tool is plugged in and a request is made.
I would like to remind our readers that the global side of the scan tool yields a tremendous amount of data that I feel should be initially accessed in the event of a MIL. The 10 modes are shown in Fig. 4. We wrote an article previously in Automotive Service Professional covering in detail the importance of the 10 modes available on the global side of the scan tool.
The framework of this article will focus on the data and functions available on the enhanced side of the scan tool on the CAN compliant Chrysler systems. First and foremost, we need to remind ourselves that Chrysler still uses the Speed Density type fuel and spark control strategy by using the MAP sensor as a major input for fuel control and spark timing. Any problem that reduces manifold vacuum will shift the MAP voltage high which caused a rich condition and retards the spark timing. See Fig. 5.
Most of us technicians know the importance of doing a network test initially on these modern-day vehicles. The network test involves checking to see if a module is online and communicating and whether or not the module has a DTC. An aftermarket scan tool test is indicated in Fig. 6 while conducting a network check. Say, for example, if the PCM is not listed it means that there is no communication with that module. You can notice in this example that no module indicated a DTC. The Chrysler Wi-Tech PC based scan tool indicates the network test is shown in Fig. 7. The modules that are colored blue show that the module is online, communicating and there are no DTCs. The modules that are colored yellow signify the modules are online but have DTCs.
On a later article we will pay a lot of attention to the TIPM module which is the dominant module in the bus circuit. This module is known as the bus master, meaning all scan data from all modules must go through the TIPM module. In addition, this module powers up nearly every component on the Chrysler CAN-compliant systems. When considering whether a Chrysler vehicle is a CAN-compliant vehicle, keep in mind that the Chrysler minivans were the last Chrysler vehicles to become CAN complaint in MY 2008.
The main menu on Chrysler scan data is shown in Fig. 8. It’s important to learn the functions and differences between the functional test menu and the system menu. Fig. 9 is an example where we select data from an individual data packet when using an aftermarket scan tool. This is important in that it streamlines the data and improves the scan tool update rate. For example, if an air fuel ratio problem exists it would be wise to select the O2 data packet.
There are major differences between aftermarket scan tools as to how their menus are displayed. Fig. 10 from an aftermarket scan tool indicates the choices available on the enhanced side of the scan tool when selecting an individual module.
When selecting the system test menu you will see choices such as live cylinder misfire tracking, the EVAP monitor, testing the Electronic Throttle Control system and others. Many of these specific tests are done during KOER conditions.
Most technicians are aware of the diagnostic value of using the graphing mode of the scan tool when analyzing a specific sensor input.
Fig. 11 is where we selected the ignition data packet. Notice the cam and crank sensor PIDs indicating in sync. In addition, the cam and crank variance indicates 3.8 degrees. Some of these PIDs can be graphed out for a better diagnostic. When doing this dynamically the sync and the cam and crank variance will not be stable until the RPM becomes stable. It’s easy to see that these PIDs are critical PIDs on the modern-day engines equipped with variable valve timing on the overhead cam equipped engines. When looking at these values dynamically in the graphing mode notice that the sync state and the cam variance will not be stable as the RPM changes in Fig. 12.
Fig. 13 is a list of adaptive resets. For example, if an air fuel ratio problem has been corrected, we would select the fuel adaptive reset function during KOEO conditions. Notice in Fig. 13 we have highlighted the misfire adaptive numerator. This function is needed in the event a cam or crank sensor, fly wheel, the PCM, a timing chain, timing belt or the engine has been replaced. Failure to do so could result in false misfire codes. It is well documented that the adaptive memory resets by using an aftermarket scan tool sometimes do not work.
Let’s say the MIL cannot be cleared; we would first try mode 4 on the global side of the scan tool. If the MIL remains on or the ABS light remains on, we are showing the manual reset procedures in Fig. 14. If doing this procedure, keep in mind that the radio, clock settings and memory seat settings will be lost.
Figs. 15 and Fig.16 show a list of the KOEO tests that are available under the functional test menu. These tests are listed under the functional test menu and most are done during KOEO conditions. On the system test menu the options are listed in Fig. 17. Many of these tests are done during KOER conditions. We highlighted the injector kill test which can be done during KOER conditions.
Chrysler began using a 5 volt bias voltage to the oxygen sensor way back in 1997 on the zirconium oxygen sensors. With the sensor plugged in during KOEO the loading effect pulls the voltage down to 2.5 volts. During KOER conditions voltages above 2.5 volts represent a rich condition while voltages below 2.5 volts represent a lean condition. Notice the oxygen voltage before an injector was disabled in Fig. 18. Now notice in Fig.19 the lean shift when an injector was disabled. In MY 2018 Chrysler began using an electronic fuel control module with an electronic fuel pressure sensor. On these systems we would simply monitor the fuel pressure drops when conducting the injector kill test.
In addition, the live misfire monitoring is available from the system test menu. Notwithstanding, remember from the Mode 6 menu on the global side of the scan tool individual cylinder misfires will be listed from the last 10 drive cycles. Fig. 20 shows where we can take control of the alternator during KOEO conditions. Most Chrysler alternators are feed side controlled, meaning the PCM will send out 12 volts to the F1 terminal of the alternator.
Fig. 21 from the engine data packet shows a 31% duty cycle command to control the alternator during idle and no electrical load. Late model Chrysler vehicles equipped with start/stop technology will be equipped with an IBS (Intelligent Battery Sensor) which is mounted on the negative battery terminal. It reports battery state of charge during cranking and running condition to the BCM who then reports the data to the PCM. A failure of the battery will disable the stop/start system and set a PO57F code. See Fig. 22.
Chrysler coils are controlled internally by the PCM. What you are seeing in Fig. 23 is the time for each coil’s magnetic field to collapse, which is essentially the spark duration period. However, we have determined that this data is good for individual coil time of magnetic collapse for comparison purposes only. When using a lab scope a good spark duration period during idle and no load conditions will be around 2 milliseconds. Notice that the No. 1 coil indicates a 0.8 millisecond spark duration period. Though this data is not entirely correct, it did indicate that the coil’s spark duration period was significantly shorter than the other cylinders.
This data was captured from a Chrysler 3.6L engine with 79,000 miles on the odometer, well short of the factory recommendation for spark plug changes. Fig. 24 is where we selected the ETC follower test from the system test menu. This test is done during KOEO conditions. Fig. 25 indicates the APP and TPS value during ½ throttle while Fig. 26 indicates the APP and TPS values during WOT conditions. The key here is that the TPS 1 and the TPS 2 voltage values will always add up to 5 volts, no matter the angle of the gas pedal if the system is performing properly. This test is done during KOEO conditions.
Chrysler has gone to variable cam timing on most of their engines beginning in MY 2012. Fig. 27 is scan data from a 3.6L DOHC engine captured at idle. Notice the scan tool data indicates the cam and crank are in sync. In addition, notice the variance values of both exhaust and intake cams. This was captured at idle where the duty cycle command to the VVT control solenoids is indicating 0%. Unlike GM, the Chrysler PCM will vary the cam timing during park conditions and off idle. Fig. 28 is cam data captured at off idle conditions while in park. Notice the 50% duty cycle command to the bank 1 exhaust cam control solenoid. The data also indicated the actual and desired position of the cams in degrees of crank rotation. Fig. 29 indicates some important data related to the variable cam timing system as in VVT oil pressure and VVT oil temperature.
There are two types of EVAP Systems as seen in Fig. 30. These two systems are remarkably similar. The NVLD (Natural Vacuum Leak Detection) is a sealed system during KOEO. The PCM conducts a small leak monitor during an over-extended cold soak during a key off condition. As the EVAP system cools down and is sealed, a natural vacuum builds. When a value of 1 inch of water vacuum is reached, a vacuum switch closes and pulls a voltage supplied to the vacuum switch to ground. When the PCM sees this voltage pulled to ground the small leak monitor has passed. If the vacuum switch never closes and the voltage remains either 5 or 12 volts, the PCM will run the EVAP monitor on the next drive cycle by ramping up the duty cycle command to the purge solenoid, thus building vacuum and closing the vacuum switch. At that point the PCM turns off the purge solenoid which is now closed. If a leak exists, vacuum will bleed off and the PCM will set a medium or large leak code. If the system is totally sealed and vacuum remains, the PCM will energize the NVLD solenoid to bleed off the excessive vacuum. Since the NVLD solenoid is closed in a de-energized condition the system is sealed during KOEO conditions. When smoke testing these systems, the large rubber hose would need to be pinched off since some smoke machines may produce more than 6 inches of water and a pressure relief valve will open and bleed off the excessive smoke machine pressure. See Fig. 31. A schematic of the NVLD system is indicated in Fig. 32.
Fig. 33 indicates that an EVAP monitor is available from the scan tool to do a service bay EVAP monitor. If an EVAP code exists, it must be cleared before running the service bay EVAP monitor. If the code repeats, then a hard code exists. The problem here is that the EVAP monitor cannot detect a small leak code. In Fig. 34 the screen shows the results from the service bay EVAP monitor as the vacuum switch indicates closed.
Fig. 35 shows a layout of the ESIM (Evaporative System Integrity Module) unit. This unit is part of the canister unit. It contains two weights, one small and one large. The small, weighted check will seal the system and then vent vacuum above 4 to 6 inches of water. The large, weighted check valve is designed to open and vent fuel vapors to the canister like during a refueling process. During key off conditions the ESIM system is sealed. As the fuel tank cools down, a natural vacuum is generated. When the vacuum reaches 1 inch of water the vacuum switch will close which pulls the voltage to ground. This means that the small leak monitor has passed. If the vacuum switch never closes, then on the next drive cycle the PCM will ramp up the duty cycle command to the purge solenoid thus building vacuum and forcing the vacuum switch to close. The PCM will turn off the purge solenoid which locks vacuum in the EVAP system. Depending on how long it takes for the vacuum to decay, causing the vacuum switch to go back to the open position, the PCM can time the value and determine whether a large or medium leak exists. When smoke testing this system, the large vent hose coming off the canister must be pinched off.
Hopefully we conveyed the robust data and functional tests and system tests available on the Powertrain side of the Chrysler/Jeep systems. In a future article we hope to cover the vast data from the TIPM module and functions and data from the TCM.
The industry is better because of your commitment.
About the Author
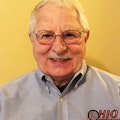