Gasoline Direct Injection (GDI) engines are becoming very popular on GM, Ford, Honda, Lexus, Hyundai, Kia models, as well as those by many European manufacturers. The reason some manufacturers are leaning toward GDI engines is because they offer an increase in fuel economy, lower emissions and an increase of engine torque and horsepower, even in small-displacement 4-cylinder engines. This occurs because the compression ratios can be increased, and the danger of detonation has been nearly eliminated.
As you already know, the GDI systems inject fuel directly into the combustion chamber instead of into the intake runners. The drawback here is that we no longer have the advantage that PFI (port fuel injection) systems offer where fuel was sprayed into the back of the intake valves, which supplied the solvent effect and kept the back side of the intake valves clean. Unfortunately, the GDI systems do not offer us this advantage. Oil vapors from the PCV system will accumulate on the back side of the intake valves which impedes the engine’s ability to breathe. The GDI engines that are equipped with variable valve timing systems can suffer from these valve deposits due to the valve overlap that occurs at off-idle conditions. This easily occurs on GDI engines when the car owner ignores the oil change intervals, or the wrong API and SAE spec oil is used.
Virtually every GDI engine manufacturer I have researched highly recommends premium synthetic oils. The owner’s manual would be the go-to place for this information. Ford, for example, will actually recommend 10,000 mile oil change intervals. Remember, this applies to normal driving conditions and we know that there is no such thing as normal driving conditions on America’s roads. And second, most of us technicians would never agree to that extended oil change interval.
Two manufacturers — Ford and Lexus — have addressed this problem by equipping some of their GDI engines with an additional PFI injection system. The PFI injectors are pulsed under certain engine conditions which allows the solvent effect on the back of the intake valves. It is critical here that the car owner is aware of the importance of using a brand of fuel known as Top Tiered Gasoline. You can do a Google search for Top Tiered Gasoline and find out what brand of fuel meets these standards.
Carbon buildup on the back of the intake valves has been a major issue for the manufacturers of GDI engines. The carbon deposit problem can be attributed to vaporized oil from the PCV system. See Fig. 1. Some Lexus dealers include a can of MOA on every oil change from the folks at BG Products. This formula helps prevent this oil vaporization problem that occurs at higher engine temperatures. Ford, for example, has never addressed this issue nor does Ford recommend intake cleaning procedures or any fuel additive to aid in preventing the carbon buildup problem.
Another problem GDI systems can suffer from is carbon buildup in the compression ring land areas which can prevent the compression rings from expanding, causing a reduction of compression. See Fig. 2. This problem is not unique to GDI engines. I have seen this problem many times on high mileage PFI engines. I have personally done the intake cleaning followed by a 30-minute cold soak period on high mileage PFI engines and gained 20 to 30 PSI increase in compression values. I have always allowed a cold soak period to allow the chemical to break the molecular bonding on the carbon. Both problems are a direct result from the car owner ignoring proper oil change intervals and using lower quality fuel.
I have always endorsed intake cleaning even as an annual maintenance procedure. The danger here concerns doing the procedure on turbo-equipped engines where carbon could break off and enter the turbo blades. (Chemically cleaning through the intake system will have little effect on the extreme carbon buildup problem seen in Fig. 1.) The folks at BG Products have a kit to address these concerns. See Fig. 3 and Fig. 4.
The procedure requires removing the intake manifold. On the intake valves that are closed, insert a few ounces of chemical known as 44K. After a few minutes of cold soak use the large wooden toothpicks to break away the carbon. The kit includes a wire brush to scrub the back of the intake valves and the intake runners, and there are a bunch of wire ties in the kit. They can be inserted into a drill with the pointed end inserted in the drill to scrub the intake runners. Obviously this procedure is going to be labor intensive.
Those of us who have a bore scope can easily confirm the carbon problem.
Once the carbon is broken loose be sure to blow the loose carbon out. You would need to do this to prevent carbon from entering the turbo blades on the turbo-equipped engines upon engine start up.
A mechanically driven, electronic controlled, high pressure fuel pump driven from the camshaft is the heart of the system and will generate fuel pressure exceeding 2,000 PSI under WOT conditions. The injectors pulse fuel into a pressurized combustion chamber.
A 12 volt injector will not generate a strong enough magnetic field to pulse fuel into this pressure environment, or to overcome the high fuel pressures in the rail. The GDI injectors are supplied with a 65 volt charge from capacitors inside the PCM or a FICM module found on the Honda V-6 engine.
When specifically addressing these systems, fuel pressures on the low side and the high side under all operating conditions need to be monitored. The GDI systems will have a low side fuel pressure sensor and a high side fuel pressure sensor. It’s obvious that if the low side fuel pressure is too low, then the high side fuel pump cannot perform properly. The good news here is that both the low side fuel pressure sensor and high side fuel pressure sensor can be easily monitored via scan data.
The high pressure pump is mechanically driven by lobes on the camshaft. The GM systems use three lobes on the camshaft while Ford uses four lobes. Most other manufacturers use a three-lobe camshaft. The high pressure pump is mechanically connected to the camshaft with a cam follower. There have been many cases where the cam lobes are worn along with the cam follower. If you replace the high pressure pump, use a magnet to pull the cam follower out and inspect for wear. Fig. 5 shows some examples of worn cam followers. You can be assured when noting this that the lobes on the camshaft are also worn and the camshaft would need to be replaced.
One of the first things to do when a GDI vehicle comes in with a lack of power complaint is to check the oil level. If the oil level is over full, this could be a strong sign that the high pressure pump is internally leaking fuel into the crankcase. If this occurs it also means the high pressure pump may not be able to generate enough high fuel pressure under heavy load, which is going to indicate lean fuel trim values and a loss of power.
The low side fuel pump provides low side supply pressure to the high side fuel pressure pump. Most of these low side fuel pumps are electronically controlled by a fuel pump control module. These pumps are not supplied with a constant voltage source. The GM fuel pump control module bangs the fuel pump 25,000 times per second, while the Ford fuel pump control module bangs the fuel pump 6,000 times per second with hot run voltage. Both fuel pump control modules receive a duty cycle signal from the PCM. As the engine load increases, the PCM will increase the duty cycle command to the fuel pump control module. This data is available via the scan tool. As the duty cycle command signal from the PCM increases, the fuel pump control module increases the on-time to the fuel pump. The low side supply fuel pressure is normally in the 50 PSI range, while the high side pressure will be in the range of about 500 PSI under idle or light load conditions. The high side fuel pressure will proportionally increase as engine load increases. During WOT conditions the high side fuel pressure can easily exceed 2,000 PSI. In the event of a hard failure of the high pressure pump, these systems are actually designed to start and run just from the low side supply pressure — although not really well.
If the high pressure pump is changed, always inspect for any wear on the cam follower, and never reuse the high pressure line that connects the high pressure pump to the injector rail. If the high pressure fuel sensor is removed from the rail it is highly recommended to replace it. Keep in mind that there is extreme pressure in the rail, so bleed off the fuel pressure before breaking the high pressure line. This could be done by removing the fuel pump fuse or the fuel pump relay and then starting the engine. When the engine runs out of fuel and dies it would be safe to break the high pressure line.
The P1219A or P1219B are common DTCs on these systems. The code is for individual cylinder fuel control. Take a look at the enable criteria for the P219A or P219B code in Fig. 6.
The code does not point to a specific cylinder but rather to which bank the rich condition occurred in. The PCM does not have the ability to identify what cylinder is causing the rich condition. Every time I have seen this code on a GDI engine it was due to an injector leaking fuel from carbon build-up in the pintle and pintle seat area. Normally this can be confirmed by monitoring the fuel pressure bleed-off during a key off condition.
All GDI engines are designed to maintain key-off fuel pressure for at least five minutes. You should also be aware that a fuel pressure bleed-off can be caused by a faulty high pressure pump. Don’t forget to always check the oil level.
For those of you who have a four-gas infrared unit, removing the spark plugs and sniffing out the combustion chamber of each cylinder would be a good test. Elevated hydrocarbons would pinpoint the leaking injector as well as a wet spark plug.
Let’s take a look at a case study from a P219A code. This is a case where a judgement call needs to be made. Using the scan tool, we conducted a fuel pressure drop test in Fig. 7. Notice two injectors indicated 68 PSI. We notified the car owner that the first step was to try chemically cleaning the injectors through the injector rail. You cannot guarantee this would be the fix. The alternate fix would be more expensive, involving replacing the injectors. Now let’s look at the scan tool reading after we chemically cleaned the injectors in Fig. 8. Did you notice the good test results?
The Honda V-6 engines will have a (FICM) fuel injector control module mounted on the intake manifold. This module contains the capacitors that charge all the injectors with 65 volts. As in all GDI engines, the injectors are sequentially ground-side controlled by the PCM. On the V-6 Honda engines the PCM will send a TTL (transistor to transistor) signal to the FICM module to control each injector on time.
We recently had a tech call from another shop with a Honda Pilot with a P219A code. The technician made a mistake by replacing the FICM module. We advised him to scope the TTL on-times from the PCM to the FICM. The TTL on-times for bank 1 indicated 0.4 milliseconds while bank 2 indicated 0.8 milliseconds. This tells us the PCM was trying to lean out the injectors on bank 1. The cause was a leaking injector on bank 1.
The high pressure fuel pump again is mechanically driven by the camshaft and electronically controlled by the PCM.
Fig. 9 shows a lab scope voltage waveform and an amperage waveform. Some high pressure pumps are ground side controlled by the PCM while others are feed side controlled by the PCM. The clue here is that by using a current probe we could clamp around any one of the two wires to obtain an amperage waveform. The resistance value of control solenoid is very low in the range of 0.5 ohms. The PCM will control this solenoid with an on/off frequency signal at about 4,000 hertz to limit the current flow values.
A good amperage waveform will only verify a good control circuit and will not help in verifying the mechanical integrity of the high pressure pump.
Fig. 10 shows a cutaway of the high pressure pump, the control solenoid, the cam follower and the three-lobe camshaft on a GM Ecotech engine.
A picture of a GDI injector is shown in Fig. 11. The compression seal at the bottom must be replaced if the injector has been removed. A seal installer is indicated in Fig. 12. The compression seal must be installed dry. The OTC tool kit includes an injector puller, an injector bore brush and an injector seal installer.
When monitoring fuel pressures on these engines, the scan tool may not show you the fuel pressure values in the King’s language. A conversion chart is indicated in Fig. 13, using a multiplier to convert a bar value or a MPA value to PSI.
As we stated earlier, the GDI injectors are capacitively charged with 65 volts and are ground side controlled by the PCM or the FICM module on the Honda V-6 engines. Noid lights and test lights will not work to determine if an injector drive signal exists when faced with a no-start. If doing a voltage trace with a DSO, you must use two channels of the DSO (one channel on each injector wire). Access to the injectors is not possible because they are buried. The easy access point would be at the harness or at the PCM. The two injector wires are wound around each other to counter the opposing magnetic fields. An injector pattern is indicated in Fig. 14. The blue indicates the injector was charged with 65 volts. The red trace indicates the injector was ground side controlled.
The yellow trace indicates a 10 amp value when the PCM supplied the ground. Moving to the right you can see the injector was again charged with 65 volts but the PCM did not supply the ground. You can see the yellow amperage trace did not indicate any current flow since the injector was not supplied with a ground by the PCM. It’s easy to see that using a current probe to check for an injector drive signal would be the preferred way. The current probe could be clamped around either of the two wires of the injector circuit. When an air fuel ratio code exists or a fuel pressure code exists, it can be beneficial to always note the freeze frame data for fuel pressure values. Fig. 15 indicates good fuel pressure values from our case study regarding the P219A code. Additional freeze frame values are indicated in Fig. 16. Note the PCM detected the first failure 217 miles ago while the last failure occurred 252 miles ago. In addition, note that there have been two failures since the first.
Now take a look at a good test drive on a V-6 Ford during a WOT acceleration in Fig. 17. Notice that the high pressure exceeded 2,100 PSI and the desired high pressured fuel was a near match.
Some manufacturers such as GM allow us to take charge of the command from the PCM to the fuel pump control module. In the example in Fig. 18 we increased the duty cycle command from the PCM to 37% and you can see the increase on the low side fuel pressure to 57 PSI.
For those who know the diagnostic value of current ramping conventional fuel pumps, be aware that the modern day fuel pumps are not supplied with constant voltage source, so the amperage waveforms will look different than that of the conventional fuel pumps.
And, the current flow values during idle no load conditions will be close to 3.5 amps. See Fig. 19.
In Fig. 20 notice that during an acceleration condition the current to the fuel pump peaked at nearly 8 amps. You can actually see the engine load conditions change during transmission shift points. This verifies how tight these systems are. The fuel pressure on the low side remained constant.
A GM vehicle with the 2.0 Ecotec engine came in with a MIL and two codes: P0087, and an additional code of P0089. See Fig. 21.
It’s important to note these two codes are performance codes. They are not a circuit type code or a plausibility code. Using our scan tool we must first confirm that the low pressure side is performing properly. With that established, we now focus on the actual high side pressure and the desired high side pressures. Notice the scan data capture in Fig. 22.
The bottom trace indicates the PCM is ramping up the duty cycle command signal to the high pressure pump control solenoid. The desired high side pressure was 2,175 PSI while the actual high side pressure indicated 50.8 PSI. The loss of power complaint was because the engine was running on low side fuel pressure only. Fig. 23 shows a picture of the old and new pumps. You can see the difference.
A Ford EcoBoost came in with a MIL with a DTC P0088 (fuel pressure too high). See Fig. 24. This is also a performance code. Fig. 25 shows the scan tool PIDs we selected. Fig. 26 is a scan tool capture before the symptom occurred. Now notice Fig. 27 where the APP values decreased during decel. Notice the actual fuel pressure remained high while the desired fuel pressure decreased. These examples show the value of scan data captured in the graphic mode.
Thanks for your commitment to this resilient industry. The industry is better because of your commitment.
About the Author
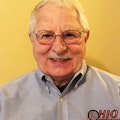