DC-DC Converters. The Solid-State Alternator
When modern hybrids came to market in 1998 (in Japan) the alternator could not be used due to “idle stop,” so a replacement was needed. Enter the DC-DC converter. (Note: we will also use the word “converter” to make this more readable.) The high voltage battery pack provides the power for the DC-DC converter, which in turn powers the 12-volt system when in “READY” mode. The DC-DC converter powers the head and tail lights, wipers, radio, windows, computers, 12-volt pumps and so on, but not the 12-volt battery. The DC-DC converter keeps the 12-volt battery charged so it can be used when the vehicle is off, in accessory, or in “Power On” mode as defined by the National Institute of Automotive Service Excellence (ASE). For this article we will use 12-volts to describe the low voltage system for easier reading. Note: Tesla has recently gone to a 16-volt Li-ion battery.
Cooling it Down
Once the DC-DC converter was chosen to replace the alternator, other challenges arose. Everything has an upside and a downside. One of the downsides is the transistors found inside a DC-DC converter get hot. That is waste heat and never a desirable trait. Both liquid and air cooling were used in the beginning but liquid coolant won out, because it was more reliable. Honda used air cooling on all their IMA designs. If the 12-volt battery was not well maintained, or was left in the car after its useful life was over, the DC-DC converter would overheat. Why? It was continually putting out more amps than it was designed to due to the defective 12-volt battery. That extra work created more heat and that is a problem for any DC-DC converter. The root cause was a failure to test and replace the small battery.
The Honda Insight went on sale in M/Y 2000 and the air conditioning system was an option. That meant that on a very hot day, if A/C was not installed, the DC-DC converter would not get the cooling it needed. The design of many air-cooled hybrid components relies on the driver to turn on the air conditioner to cool themselves down and that in turn also cooled the power electronics and the HV battery. The air that cools many high voltage parts is drawn from the cabin. The cabin air should be about 70 degrees Fahrenheit so that the DC-DC converter has cool air being driven over it by a cooling fan(s). The cooling fins on the DC-DC converter would then remove the heat from the transistors. As long as the entire system works as designed, the DC-DC converter could have a very long life as it is solid state. It has no bearings, belt or brushes to wear out, so it is possible for the solid-state device to last 1,000,000 miles. There is no preventive maintenance on the DC-DC converter other than the cooling system. Almost all DC-DC converters are now liquid cooled.
What Is Inside
If you want to know more, take the bottom steel cover off a 2004-2009 Toyota Prius Inverter. Under the cover you will find a DC-DC converter and the inverter for the 3-phase high voltage air conditioning compressor. Follow the two large diameter cables entering at one corner. They are 200-volt, DC colored orange and black. These power the MOSFETs (metal-oxide semiconductor field-effect transistor). These four transistors are connected to 200-volt DC power supplied by the high voltage battery pack. What you need to know is the high voltage DC must be changed to a high frequency AC. These four transistors switch the polarity of the DC high voltage cables that connect inside the DC-DC converter. Do not try the next example, just think of it this way.... Picture a scope connected to the high voltage battery and you have set the zero line at the middle of the scope with 250 volts above and below the center line. The time base is in one second intervals. Once you have the cables connected to the HV battery you will see a flat line at about 200-volts above the center zero line. Now disconnect the cables. What do you see now on your scope? The line is flat and at zero. Reconnect the cables in reverse order. Positive lead to the negative HV battery cable and vice versa. Now what do you see on the scope? Two-hundred-volts below the line or a negative 200-volts. OK, now do that hundreds of times per second. Remember we are only looking at voltage. When you add a current-clamp you will see a ragged looking AC sign wave. In reality a DC-DC converter starts with DC voltage and current from a high voltage battery, and converts that to a polarity switched DC that produces AC amperage. So, it is both DC and AC at the same time — DC voltage and AC current. From there the AC is lowered in voltage by the Mutual Induction Coil, then AC travels through a series of diodes, right out of an alternator in this case, that rectifies (allows the AC current to only go in one direction) and that action changes the AC to DC. There is one more device, an AC filter, that looks like a flat coil surrounded by a powerful magnet. It is there to make sure the DC power is as pure as possible. Once you see the power flow, a DC–DC converter will be simple to understand and diagnose. The non-computer-controlled induction coil was used as a safe way to achieve the goal of providing 14-volts and hundreds of amps using the high voltage system. The main difference is that “high voltage single phase AC” is manufactured in a DC-DC converter as opposed to three-phase AC that is created in a traditional 12-volt alternator with a rotating magnetic field.
Failures and Testing
The good news is the training you have had on the conventional 12-volt battery, starter and alternator will come in handy as the testing and equipment you are familiar with can be used. The normal symptom is “my 12-volt battery goes dead.” If the DC-DC converter fails, the EMV can only drive as far as the 12-volt battery has power available, just like in a conventional car. The same situation as an alternator failure, the 12-volt battery will soon run out of power and the car will stall and will not restart. Once you have an accurate description from the driver of the car at the time it failed, complete a full history of the car. Check the VIN against any recalls for service updates that may fix the problem. Software updates can fix a ”bad converter” as owners of 2006 Civic HEVs found out after the 12-volt battery went dead. Remember, even though the DC-DC converter is connected to the HV battery pack, a computer signal is required to request it to “turn on,” usually through a CAN bus. The DC-DC converter will supply the required volts and amps for the whole 12-volt system when the “READY” light is on — if the system is working as designed. If the “turn on” DC-DC converter signal does not get there, the converter will not work. A simple software issue can render it useless. Some EMVs use this strategy: if the HV battery is having a problem, such as capacity loss, out of balance, low SOC on some cells, etc., the converter will be commanded off until the HV battery issue is fixed. Do not replace a DC-DC converter until you have confirmed the HV battery is OK and the software is up to date. Can you use an EMV to jump-start a conventional vehicle? No, unless you know the systems really well in both vehicles as there are exceptions.
The Chevy Volt
The first year of production for the Volt was M/Y 2011. ACDC (my business) bought one right away in New York State as Massachusetts was not on the list. One thing seemed odd as we studied, scanned, scoped and looked over this plug-in. A traditional DC-DC converter was mounted in the trunk floor. It was air cooled, a step backwards in our opinion. Up front was one more. It incorporated the on-board charger and was liquid cooled. So why two? GM had installed two DC-DC converters a few years earlier on their two-mode hybrids, but that made sense. One was 12-volts and the other was 36-volts for their electric power steering. The new Volt had two 12-volt DC-DC converters. Why?
The rear one is used when driving and you are in the car. We call that a “dumb” converter. If this converter continues to supply current and a small 12-volt fire starts, once the driver smells something burning, it is “stop the car” and get out. This happens on ICE (internal combustion engine) powered cars and trucks as they get older and backyard untrained hackers have their fun. Usually no one dies and it makes a great YouTube video.
When your plug-in is charging in your attached garage, it isn’t so funny. The front converter is used when the Chevy Volt is plugged-in. It is a smart DC-DC converter. Not genius level, but smart. This converter knows how many amps it is sending and what is normal at that time. If it senses too much current, it stops supplying current to the car and stops charging. While the plug-in is charging, or just plugged in, the 12-volt system is working in the background keeping the support systems functioning. In the unlikely event that a 12-volt component is asking for more current than it was designed for, game over. Both the low and high voltage systems are shut down. This prevents over-heating any 12-volt part of the “powered up” system and it prevents 12-volt fires.
Summary
DC-DC converters need a healthy HV battery to power them and a properly functioning 12-volt battery too. Use all the best safety precautions when working on these high voltage components. Have a plan that makes sure you cover all the bases. Do not make anything up. Get the service information and ask questions if you do not know the system. Master your scope and current probe so you can make sure your repair is done exceptionally well and your diagnosis is complete.
Electric vehicles are our future. You may feel they are not needed, or this is some huge mistake. I have had many skeptical technicians in our classes and I address their concerns about the future as best I can. There have been more the last few years than ever before. What your personal views are will not change the numbers of EVs that will be sold in the future by much more than a fraction of a percent. The momentum of going electric cannot be stopped now.
I have had the privilege of being a part of this 25-year transition away from burning fossil fuels to powering my cars and motorcycles with electricity. I am fortunate to live where the grid gets cleaner every year. Being ready for the vehicles that will come into your bays will change your daily life as a technician. No more fumes, no more burned flesh on a hot exhaust system, no oil changes or gasoline dripping down your arm as you replace a fuel line. Welcome to the new generation of powertrains. It will not be as bad as you may imagine. You might grow to like these quiet cars.
Glossary of terms
- MOSFET: Metal Oxide Semiconductor Field Effect Transistor
- IGBT: Insulated Gate Bi-polar Transistor
- SiC MOSFET: Silicon Carbide Metal Oxide Semiconductor Field Effect Transistor
- EMV: an ACDC vehicle term that includes all Vehicles with High Voltage Drive Systems
- HV: High Voltage
- M/Y: Model Year
- HEV: Hybrid Electric Vehicle
- PHEV: Plug-in Hybrid Electric Vehicle
- EV: Electric Vehicle
About the Author
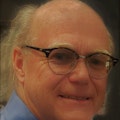
Craig Van Batenburg
Craig Van Batenburg is the CEO of ACDC, a hybrid and plug-in training company based in Worcester, Mass. ACDC has been offering high voltage classes since 2000, when the Honda Insight came to the USA. When EVs were introduced in 2011, ACDC added them to their classes. Reach Craig via email at [email protected] or call him at (508) 826-4546. Find ACDC at www.FIXHYBRID.com.