Chris Taylor named inaugural winner of Best Young Tech Award
When Chris Taylor was 14 years old, his uncle gave him a 1998 Ford Mustang that he started fixing up and teaching himself how to do basic repairs. Before too long, he was swapping out the V6 engine for a V8 and then installing a cam and changing the rear differential gear ratio.
“It started when I was young. I always loved play with Hot Wheels cars and I used to pretend I was in my own car, shifting gears and making car noises,” Taylor recalls. “I grew up in Jamaica and then I came back here and I always hung around a lot of people who are into cars.”
When the time came to choose a career path, Taylor didn’t know what he wanted to do, but he knew he loved cars, so he followed that passion to Universal Technical Institute in Orlando and became an automotive technician. Upon graduation, he received his Ford FACT certification and was hired at a Ford dealership. Today, he’s a technician in the fleet management division at Polk County in Florida, where he fixes everything from the county’s Ford F-150 fleet to ambulances or a boom on a utility truck.
Taylor is the inaugural winner of the PTEN and Motor Age Best Young Tech Award, designed to honor technicians aged 35 or younger who are moving the service repair industry forward, excel in their current role, and are passionate about their work. Taylor, age 31, stood out to the judges for many reasons, especially his strong work ethic.
“I even tie it back to being that 14-year-old tackling that Mustang project and the stuff he did was not just changing oil! That was serious stuff for someone who had no training. I saw that initiative as a common thread throughout his career so far,” says Mike Pressendo, chief marketing and strategy officer at the TechForce Foundation, who was one of the judges for the award program. “He doesn’t sit back and wait to be told to 'Go learn this, or 'Do that'; he just jumps in and goes after it."
Taylor’s work ethic was evident to Robert Biller, fleet management director, the day he started working in his division. He was immediately put on the shop floor and assigned work orders on vehicles and equipment that he had little or no experience with, most notably the large M2 Business Class Freightliner chassis used for the county’s ambulances. Taylor did not hesitate: he went to the OEM manuals and researched the issues he was dealing with, and also dove into the NFPA books to ensure he was repairing the life safety equipment properly.
“Whenever he is faced with a job or equipment where he has limited exposure or experience, he knows his limitations and goes to the correct reference material in order to do a proper repair,” Biller says. “As information gets passed on by mouth, it gets less and less accurate… So when you read the manual, you learn how to do it correctly. It’s a refreshing mentality in the shop… and has resulted in his knowledge level rising much quicker than his peers.”
Leading by example
Taylor’s quality of workmanship is another element that stood out to the judges. He always performs a very in-depth inspection of the vehicles he is assigned to repair. He builds lists of items that need attention and adds them to the list of repairs on the vehicle's work order. A simple front brake job may turn into calipers, brake lines, or power booster job just by identifying pending issues. Shop-visit frequency is one of the division’s key performance indicators, so identifying issues before they require another shop visit is a very important boost to the division’s measured efficiency, Biller says.
“The other guys would have something come in, say, for brakes and they would take those wheels off and slap some pads and a rotor on there and get it back on the road as fast as possible, missing the brake line, leaky shock and different things that are going on under there. Chris seems to be very adept at catching that stuff and taking care of it when it’s in the shop,” he says.
Technicians are always aware of what the other technicians in the shop are doing, and his co-workers have noticed Taylor is spending a bit more time going beyond the initial problem verification and have started to follow suit, adds Biller.
“Now the other guys have decided maybe there’s not as much honor in getting in and out as fast as possible as is doing an accurate job, he has two younger techs working right beside him and they started to adopt his ways, which is really nice because usually they adopt bad habits!” he laughs.
But Taylor notes he did face some resistance at the start from other co-workers when he was taking his time and not just flying through the repair. They would often ask him why he was doing this or that, but Taylor stuck to his committed to quality.
“In the end, you start seeing the respect. You will see a customer who wants only you to work on your car. In the end it pays off,” Taylor says, adding that he was taught by an instructor in the Ford program to always think of the vehicle you are repairing as one that will be carrying your own family members. “So I always take that extra step because it’s ingrained in me to do the best I can,” he says. “And I’ve always been particular. I’ve always been that type of person that takes pride in what I do.”
In addition to his Ford FACT training, Taylor has a Class B commercial driver’s license and an impressive list of certifications under his belt, including the following:
Automotive Service Excellence (ASE):
- A1 Certificate for Automotive Engine Repair
- A5 Certificate for Brakes
Emergency Vehicle Technician Certification Commission:
- E0 Ambulance Maintenance, Inspection and Testing
- E1 Ambulance Design & Performance
- E3 Ambulance HVAC Systems, E4 Ambulance Cab Chassis and Powertrain
- F1 Maintenance, Inspection & Testing of Fire Apparatus
- L1 Law Enforcement Vehicle Installation
Pressendo notes that Taylor’s pursuit of continued education and credentials really stood out among the other Best Young Tech Award nominees.
“If you have a certification, you demonstrate that you have the knowledge and understanding. You can say, ‘I have read the manual and I did this online training,’ but did you get it? Can you apply it? To me that’s what certifications layer on,” Pressendo explains. “Knowledge is valuable, shops look to the person who has the knowledge to fix the challenges problems… I would also say it translates to better income too.”
When asked how he finds the time to keep adding certifications, he says it can be hard, but he makes the time because he knows it’s beneficial to him.
“I like to learn new things every day,” he says. “If you’re not learning, you’re not growing, and I want to grow. I try to soak up everything like a sponge.”
Additionally, Taylor loves to learn new things so he can share that knowledge with his co-workers.
“I know what it’s like to work in a dog-eat-dog environment where no one helps you and you feel alone, so I try to help everyone. I try to be there for them. I feel like we’re all a team. I don’t think about myself; I think about everyone,” he says.
Biller says Taylor can often be found showing the newest technicians how to use the electronic diagnostic equipment to identify customer complaints. He is helpful, friendly, and is setting a great example for the younger technicians at the shop.
Looking down the line, Taylor hopes to be in a management position one day and he is eager to learn more about the “business side of things.” Biller has no doubt he will continue to grow within the organization and will have a very successful career at Polk County.
“He is kind of guy you hope comes out of tech school,” says Biller. “He does what he's told, he does it very well and then he goes above and beyond… He’s always working to improve himself as well as those around them. He’s a well-rounded technician and a pleasant person to work with. He’s everything you look for a technician and then some.”
Sponsored by:
RUNNER-UP
Eduardo Robles
Master automotive technician at the City of Ventura
Age: 31
Eduardo Robles works on police patrol vehicles for the City of Ventura in California. He completes modifications, repairs, computer programming, and demobilizing. Robles works at a pace that is methodical and smart, and the work he completes is “simply outstanding with impeccable results,” according to Frank Palmer, fleet services supervisor at the City of Ventura. He has a can-do attitude and he comes to work with a smile on his face, elevating those around him. He meets challenges head on and is laser focused when solving problems.
“His continuous learning attitude and positive demeanor is highly contagious and appreciated,” Palmer says. “I have 30 years of experience in fleets and this kind of talent only comes by once in a career.”
ADVICE FOR YOUNG TECHS
From Mike Pressendo, TechForce Foundation
- Embrace technology: The advent of the computer assisted technology and the ability to diagnose those things is huge.
- Gain EV knowledge: EVs will be out there, so anybody with that advanced knowledge and aptitude will do well.
- Take safety seriously: The electricity in EVs can be lethal, so know how to work on them safely.
- Have excellent customer service skills: Whether that’s with your internal customers or external customers, if you have good communication skills and are inclined toward providing excellent customer service, that will be a differentiator for you.
GRAND PRIZE
As the winner of the Best Young Tech Award, Chris Taylor received the following prize pack:
- Roundtrip flight and lodging for two nights for the AAPEX/SEMA shows in November in Las Vegas
- A trip for two to the STX Supplier and Training Expo in March
- $5,000 in Milwaukee tools
- Autel MaxiSYS MS906TS scan tool
About the Author
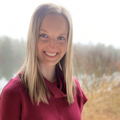
Amanda Silliker
Amanda Silliker is the former editorial director of the Vehicle Repair Group at Endeavor Business Media. She oversaw five brands — Motor Age, PTEN, Professional Distributor, ABRN, and Aftermarket Business World. Prior to her tenure with Endeavor, she had over a decade in B2B publishing at Thomson Reuters, ranging from writing and editing content for print and web to managing awards programs and speaking at conferences and industry events. Connect with her on LinkedIn.