While Tire Pressure Monitoring Systems (TPMS) date as far back as the 1980’s when they first appeared on higher end European vehicles, their increased use has been driven by the federal government beginning in 2000 when the Transportation Recall Enhancement, Accountability, and Documentation (TREAD) Act was enacted. The TREAD Act was a result of investigations into an abnormal number of tire failures involving Firestone tires installed on Ford Explorer vehicles following several tragic vehicle events
The mandate for TPMS in the U.S. came from the Department of Transportation (DOT) in 2005. The federal regulation requires all 2008 model year vehicles and newer under 10,000 gross vehicle weight rating (GVWR) be equipped with a tire pressure monitoring system that detects when one or more of a vehicle's tires is significantly under-inflated and illuminates a low tire pressure warning indicator light.
The events leading to the TREAD Act were serious and resulted in brand damage for both Firestone and Ford Motor Company. There are several benefits to the reporting and accountability requirements where manufacturers are required to disclose deficiencies in their products that could lead to a safety condition. The Ford and Firestone events primarily involved vehicles with a high center of gravity that suffered tire failures that were linked back to low tire pressure.
TPMS sensors
Today, we have two types of tire pressure monitoring: direct (dTPMS) and indirect (iTPMS). A direct measurement system measures the tire pressure via a wireless pressure transducer mounted inside the tire.
Indirect systems make inference to tire pressure by measuring the rolling circumference via individual wheel speed sensors. These are usually part of the anti-lock brake system (ABS). Basically, when the tire pressure is low, the rolling circumference shrinks, resulting in a shorter period of time per revolution. Algorithms are used to monitor these systems so that they’re able to properly report trouble to the driver.
There are a couple of downsides to using iTMPS, however. First, the system is unable to identify and report which tire is actually low. Second, if all four tires are equally low, the system will be unable to alert the vehicle operator. As per the regulation, all TPMS are required to display a driver alert warning when the tire pressure deviates by 25 percent from the recommended pressure. Technicians need to be especially cognizant of tire size when servicing iTPMS sensors.
“On iTPMS systems, one needs to be aware of the variance in tire diameters,” says Matt Fanslow, technician and shop manager at Riverside Automotive in Redwing, Minnesota. “We look closely at the tire circumference before diving in on diagnosing these systems.”
TPMS sensors have their own battery power supply and communications are usually handled by the same wireless receiver used for keyless entry. The wireless receiver typically communicates tire pressure data via the CAN so that the onboard systems can leverage that data for safe vehicle operation. Sensors generally transmit information once every 30 minutes when idle/parked. The update rate typically increases to about 1 Hz when the sensors can identify that the vehicle is no longer at a standstill. For most systems, this threshold occurs at speeds greater than 30 mph.
When replacing TPMS sensors that are damaged, worn, or have low batteries, technicians can choose either OEM replacements or universal aftermarket units. There are reasons to consider each option.
“We use Autel MX1 sensors unless they [are not compatible], and then we go OE,” Fanslow says. “I would guess that the Autel sensors work about 95 percent of the time.”
On the other hand, Kirk Holland, owner of Gladney Automotive Solutions in College Station, Texas, says his shop uses OEM sensors even though universal sensors are less expensive. He notes they have had some sensors fail to learn IDs, or just fail overall.
Thanks to the various options available on the market, it’s becoming more common to see older model vehicles equipped with TPMS that have both OEM and aftermarket sensors. This can present a new challenge to technicians servicing the vehicle.
“Twelve years into TPMS [being government mandated] the chance for a vehicle having multiple sensor types installed is increasing,” says Scot Holloway, CEO and general manager of Bartec USA. “Vehicles with a combination of OE and aftermarket sensors present a unique challenge for the service provider. Do they have the right service kits or replacement parts to properly service that car or truck? Early GM TPMS sensors only ‘activate’ with a magnet, not a TPMS tool, [for example]. The technician needs to know this, otherwise they could get a false diagnosis of a TPMS sensor.”
Whether they’re OEM or aftermarket, TPMS sensors need to be able to withstand harsh environments and are typically designed to last 10 years or 100,000 miles. Given this goal, think about how one should be treating these sensors during service. Things like valve stem caps and proper torque of the Schrader valve and mounting nut are equally important.
“[We see] lots of corrosion issues leading to premature sensor failures,” Fanslow says. “I believe that this is often caused by not using the proper tools, over-torquing, and not replacing seals and [valve stem] caps.”
Additionally, it’s important to pay attention to the vehicle and tire speed ratings. According to a Schrader International service bulletin TSB-2012-05, dated April 11, 2012, if you have a vehicle equipped with tires that have a speed rating greater than 115 mph (1852 kph), you must use aluminum clamp-in valve stems as opposed to rubber, snap-in stems. Just because the vehicle arrived with rubber stems doesn’t mean that they’re correct.
Technicians should always follow the manufacturers recommended procedures when servicing TPMS sensors. Valve stem service is critical, requiring the proper torque be used when assembling. There are special service tools technicians can take advantage of so that the proper torque levels can be achieved each and every time. Here are a few to consider:
- Schrader TPMS Nut Torque Tool with Sockets, No. SB-20138
- Schrader Valve Core Torque Tool, No. 20141
- Steelman TPMS Valve Core Torque Tool, No. 96229
- Steelman TPMS Basic Service Tool Kit, No. 96254
- Lisle Valve Core Torque Tool, No. 18810
Additionally, there are numerous service kits available today that will allow you to deliver professional service, as shown in Figure 1.
TPMS service
With some customers, half the battle when it comes to TPMS service is getting them to understand the importance of properly maintaining the system.
“We have lots of fleets and retail customers that don’t see the value [in TPMS service],” Gladney Automotive’s Holland says. “We push it pretty hard [because it’s] a safety item.”
The next challenge can be having a clear understanding of the system operation for the vehicle being serviced. The best source of this information can be found within the service information. However, one should be aware that highly useful information can also be sourced from the vehicle’s owner’s manual. When troubleshooting TPMS, technicians should always think about how the overall system functions. Keeping this information straight can be difficult, however. Different vehicle manufacturers design their TPMS differently, so each can present unique challenges.
“Toyota is a regular suspect when it comes to TPMS concerns,” says Edmond Francavilla, TPMS technical support representative at Autel. “Most of them just seem to give inexperienced TPMS users a hard time. There has been some confusion with relearn procedures and it needing to be an OBD functionality. Some of the new Toyotas are going to an automatic relearn procedure. [There is also] a ‘TPMS reset’ button that needs to be pressed after a relearn on certain SUVs and trucks. Some models even carry the option for a main and secondary set. All of this combined with a difficult sensor to replace can definitely be confusing, but we regularly explain that the ‘Copy by OBD’ feature is the easy resolution to avoid the relearn issues by combining both the sensor ID programming and sensor position relearning steps into one step easily completed through the TPMS tool.”
Other Asian automakers have TPMS systems that can be similarly confusing to work with, confirms Bartec’s Holloway. Lexus and Honda both require special procedures when initiating a relearn.
“Lexus vehicles with the ‘TPMS button’ can be confusing the first time doing the relearn,” Holloway says. “Making sure the button is in the proper position before starting the relearn is the key. There are few Honda vehicles that require a sensor mode change before relearning. Both scenarios are manageable providing you pay close attention to the procedure on the tool or in the TIA Chart.”
Another consideration when servicing TPMS is that on many vehicle makes, the keyless entry system is likely part of the TPMS, so it’s important to think about where the keyless entry module is located on the vehicle and whether it might be subject to a harsh environment or extreme conditions. The keyless receiver module may be located in the trunk where fluids may have been spilled or where the body seals may have failed allowing moisture entry. We all know what happens when electronic components are introduced to moisture. An example is shown in Figure 2.
TPMS tools
The engineering that goes into TPMS sensors is pretty amazing. Data parameters such as air pressure, temperature, battery condition, and hex ID can typically be found on modern systems as shown in Figure 3.
Retrieving this data, however, requires the use of dedicated TPMS tools. In most cases, the data is available using a TPMS tool without any cabled connection to the vehicle, of which there are many on the market. Riverside Automotive’s Fanslow says his shop utilizes the Autel MaxiTPMS TS508 as well as the ATEQ VT55, while Gladney Automotive’s Holland is more familiar with the Bartec Tech400 and 500. Whichever tool a shop uses, it is important to fully understand the TPMS system and how to use the TPMS tool before going to work on a vehicle.
“Tire repair techs commonly confuse programming and relearn, which [can cost them] a lot of time,” Autel’s Francavilla says.
Bartec’s Holloway adds that technicians are not always aware that sensors even need to be reprogrammed at all, noting that the company’s technical support agents frequently walk the technicians through the process of programming a sensor.
He adds that placard programming is another area that can go overlooked but is imperative to proper operation of the system.
“Placard adjusting is part of keeping a TPMS operative,” Holloway says. “If a customer wants to upfit his truck from P rated tires to LT tires, chances are the recommended inflation pressure [for proper load carry capacity] will increase. This is a direct impact on the TPMS. The TPMS light is triggered once 75 percent of placard pressure is hit. If a truck tire is now inflated to 50 psi [the recommend inflation pressure] that tire will be half flat before you get the TPMS low pressure light. It’s a must to reprogram the placard in order to keep the TPMS operational.”
Most service tools today will guide technicians through the various test and service routines. If a tool doesn’t have the specific vehicle listed and you want to query a sensor, technicians can always try selecting different vehicles that use the different frequencies. Most systems today operate at 315Mhz or 433Mhz. Trying either of those may provide access to the sensor information. The reset/relearn procedures would not be available, but the above step may help a technician get through a particular situation.
Just as important as understanding how to use the tool is knowing how to keep its software up to date. Items such as vehicle coverage and new features are frequently updated, so keeping the most current software on the tool is critical.
“Updating the tool software has to be number one [most common issue we deal with],” Francavilla says. “Many technicians struggle with … things like downloading, installing software, and using it to update their tool. Sensor coverage, vehicle coverage, and new features are all affected if the tool is not kept current.”
Holloway confirms the same is true at Bartec.
“Most often, the issue technicians face is process related,” he says. “With the proliferation of programable sensors, keeping the TPMS tool up to date is super critical. Often, the first thing we do on a tech support call is get their tool updated.”
Keeping TPMS tools updated is just one of many important steps when servicing this important safety system. Armed with the proper components, tools, and knowledge, technicians are able to perform TPMS service effectively, providing safe and reliable transportation for customers and efficiency for the shop.
The following resources may be helpful to those interested in increasing their knowledge and awareness concerning TPMS and general tire safety.
Resources:
- Schrader Academy: schradersensors.com/en/training-and-support/tech-training
- Tire Industry Association: tireindustry.org
- National Highway Traffic Safety Administration (NHTSA): nhtsa.gov/equipment/tires
- Federal Motor Vehicle Safety Standards – TPMS: federalregister.gov/documents/2005/09/07/05-17661/federal-motor-vehicle-safety-standards-tire-pressure-monitoring-systems
About the Author
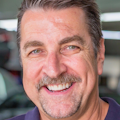
Scott Brown
Founder - Diagnostic Network
Scott is an ASE Master Certified Automobile Technician with L1, L3, & L4 credentials and has over 39 years of professional service industry experience. As an independent shop owner in Southern California and with his engagement at various levels of within our industry, he continuously strives to move the industry forward through networking, education, communications, and training. Scott is a founder of the Diagnostic Network (https://diag.net/) which was born in 2018 after he retired after 22 years at iATN, where he served as company president.
Brown is also the host of Professional Tool and Equipment News (PTEN) and VehicleServicePros.com podcast, Torque Factor. The podcast addresses the latest automotive service technologies while focusing on expanding knowledge and awareness around tools, equipment, education, and industry trends.