How Trump’s 2025 Tariffs Threaten U.S. Auto Industry
In his inaugural address on January 20, 2025, President Donald Trump promised to “tariff and tax foreign countries to enrich our citizens.” On his first day in office, he announced plans to impose tariffs on Canada, Mexico, and China, effective February 1.
Although these plans have shifted multiple times as different industries have voiced their concerns, the future consequences of Trump’s tariffs on automotive manufacturing remain significant.
Below paints a clearer picture of what Trump’s tariff timeline has looked like since January, what the current state of tariffs is, and what that means for the automotive industry in the United States.
Trump’s 2025 Tariff Timeline
According to the Associated Press’ reporting, Trump signed an executive order on February 1 for an additional 10% tariff on Chinese imports, and a 25% tariff on imports from Mexico and Canada. Per executive order, the tariffs on Mexico and Canada were set to go into effect on February 4, but were put on a 30-day pause by the administration two days later. However, the tariffs on China still went into effect.
A week later, the White House announced plans to tax all steel imports at a minimum of 25%, as well as raising tariffs on aluminum to 25%. In March, 30 days after the pause was implemented, the tariffs on Canada and Mexico officially took effect. Additionally, the government increased its tariffs on China to 20%. The next day, the White House exempted automakers from the tariffs on Mexico and Canada for one month.
On March 26, AP reported that a 25% tariff on auto imports would be imposed by the White House starting April 3. The tariffs started with taxes on fully imported cars and were set to expand to applicable auto parts in the following weeks through May 3.
On April 29, Trump signed an executive order to relax some of his tariffs on automobiles and auto parts. On the same day, the administration announced it would provide a rebate for domestic car producers importing car parts. The reimbursement is 3.75% of the value of domestically produced cars. This will then decrease to 2.5% for the second year and be phased out entirely after that.
Trump’s tariffs were implemented to bring auto-manufacturing plants and jobs back to the U.S., but so far, this has been implausible.
Sticker Shock Ahead
According to a report by USA Today, roughly half of new vehicles sold in the U.S. are assembled within the country, but even these vehicles use parts imported from other countries.
Automakers in the U.S. are highly dependent on Canada and Mexico to supply them with vital automotive parts, like engines, transmission systems, and various electronics.
The tariffs placed on these goods will leave very few automakers in the U.S. unaffected by them. Even with Trump’s reimbursement on domestically produced cars, the tariffs will still impact U.S. automakers. The increased costs on auto parts from Canada and Mexico mean increased prices for U.S. automakers, which in turn will lead to higher sticker prices on vehicles for U.S. consumers.
"The automobile sector is likely to see considerable negative consequences, not only because of the disruption of the supply chains that crisscross the three countries in the manufacturing process, but also because of the expected increase in the price of vehicles," Cornell University professor of government and public policy Gustavo Flores-Macias said in a statement to CBS MoneyWatch.
Demand for cars in the U.S. is predicted to slow as consumers look for cheaper vehicles in the used car market or seek out vehicles assembled elsewhere.
The Cost of Coming Home
Even if more automakers move production and supply chains to the U.S., as Trump intends, there are factors that must be considered. Automakers must consider the cost of labor in the U.S. For example, most vehicles built in Mexico are lower-priced models. This is because labor costs less. If production were to be moved to the United States from Mexico, the price of the vehicle would go up because of having to pay workers more.
Additionally, the timeline and cost of localization must be considered. Building new assembly plants is expensive. According to a report by CNBC, the most recent assembly plant to be built in the U.S. was Hyundai’s “Metaplant” in Georgia. This plant cost $12.6 billion to produce and took two and a half years to build.
With all the back-and-forth over tariffs and cost increases in goods and labor, auto companies are hesitant to relocate their entire supply chains and manufacturing operations. They cannot feasibly make billion-dollar relocation decisions based on policy changes that could shift again with the next presidential election.
“If you’ve ever done a home renovation, you know that anything is feasible if you put enough money behind it, right? But economically feasible is a different question,” said General Motors CFO Paul Jacobson. “It takes time. So, you’re talking investing in new physical capacity in the US, which has a very long lead time.”
Although in theory, tariffs are a great way to boost the country’s economy, there is a long path ahead to make this possible. “I’m convinced that localization is the way, but localizing new models that are built somewhere else in the world doesn’t happen overnight,” Christian Meunier, chairman of Nissan Americas, told CNBC, “It’s not going to be a matter of months. It’s a matter of years.”
About the Author
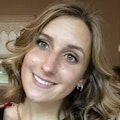
Emily Kline
Emily Kline is a Special Projects Editor for FenderBender and ABRN. She has worked in the Vehicle Repair Group at Endeavor Business Media for over 2 years, learning about vehicle repair and the automotive industry as a whole. She has a bachelor's degree in English from Saint Mary's University of Minnesota in Winona. As a writer, she enjoys her fair share of reading and has no shame using the long Minnesota winters as an excuse to stay indoors and cozy up with a good book.