Aerodynamically designed vehicles of today don’t allow much airflow into a vehicle when the windows are down, so a functional air conditioning (AC) system is crucial to driver and passenger comfort.
The automotive AC system has four major components: a compressor, a condenser, an expansion device and an evaporator. Yes, there are controls, electronics, lubricants, hoses, filters, fittings and other components, but I want to concentrate on these four major components of the AC system and some of the issues that they are creating that we are seeing in the industry.
The AC compressor — traditionally belt-driven by the engine, but now commonly run electrically on hybrids and electric vehicles — is responsible for pulling the low-pressure, low-temperature gaseous refrigerant from the evaporator. The compressor then compresses this gaseous refrigerant, raising its temperature and pressure before forcing it into the condenser. Not all compressors will cycle or have a magnetic clutch anymore. Their output displacement is now electronically controlled, usually by the climate control system. These clutchless, non-cycling compressors are always operating, even with the AC switched off. (When off, they are freewheeling and use little energy.) But if the clutchless compressor becomes internally damaged or seizes, it has a built-in breakaway device that will allow the drive-belt bearing portion of the compressor drive to rotate and not take out the entire drive belt system.
Many full hybrids and all-electric vehicles will use a speed-controlled, high-voltage, electrically-driven compressor. Special service care, safety and procedures must be observed when servicing these high-voltage units (200V DC or more). Electric compressors typically are scroll-type compressors and not the swash plate compressor design used on most engine-only driven vehicles. Also, using a scroll-style compressor saves about 20% in compressor weight.
Compressor failure from lack of lubrication is a common issue. When there is a refrigerant leak, a small amount of the lubricating oil will also be lost along with the refrigerant. With many of today’s AC systems holding tiny amounts of oil, even a small amount of lost lubricating oil can be detrimental to an AC compressor. The AC compressor has many moving parts that need to be cooled and lubricated by the oil in the AC system. If the AC system is operated with a low refrigerant charge for an extended period, the compressor can suffer unseen damage. The lack of lubrication and cooling often leads to internal damage and debris being created that will stay in the compressor until the system is recharged or repaired. The restored level of refrigerant will often loosen this debris and transport it through the AC system, causing other issues and complications. Plugged orifice tubes, restricted expansion valves and failed compressor control valves are quite common shortly after an AC system is recharged or a leak has been found and corrected.
Flushing and filters are important items to pay attention to if a compressor has failed. The accumulated debris from the failed compressor must be removed from the system by flushing. If the system is not properly flushed, the accumulated debris can quickly contaminate and destroy a new compressor or other parts of the system. When replacing a failed compressor, the proper amount and type of oil need to be installed. If the failed compressor has a drain, remove it and measure the amount of oil recovered. If there is no drain, then the high- and low-side openings will be used to drain the oil. Record the amount of oil recovered and then check with your information system on how much and the specific type that should be installed in the new compressor. If filling the new compressor with oil, use the low-pressure side and ensure that you turn the compressor shaft at least 10 times.
Some manufacturers recommend that the receiver/drier or accumulator be replaced at fixed service intervals or replaced if any major components are replaced. The moisture-absorbing desiccant material in the AC filter/drier or accumulator can only remove a fixed amount of moisture and if the system has been dormant/open or damaged for an extended amount of time, the desiccant may not be able to remove the moisture and internal corrosion of the AC system can occur.
A clutchless compressor will appear to be turning even when the breakaway device has failed, so attention must be paid to ensure the compressor is turning internally. If the belt is removed on a clutchless AC system and the pulley freewheels with little to no drag, the compressor is damaged and the breakaway device has possibly sheared. Clutchless AC compressors can often be diagnosed with a scanner. They may set codes if they have failed. Testing the clutchless AC compressor’s displacement control can be done using an amp probe and watching the current. Most VW/Audi vehicles will have a current flow to the internal control device of about 0.65A at the full cold setting and about 0.3A under normal conditions. You could also use a scope and watch the duty cycle of the signal. The full cold will have a duty cycle of about 75% and 35% when on normal.
The AC condenser is responsible for removing the latent heat from the refrigerant after the compressed gaseous refrigerant leaves the AC compressor. The compressed refrigerant gas will flow through the condenser so the latent heat, collected from the inside of the vehicle, can be transferred to the outside air via the pipes/fins of the condenser and the airflow from vehicle speed or a cooling fan assembly. Removing the heat from the gaseous refrigerant will force a change of state. The hot gas will become a hot liquid as it leaves the condenser.
The location of the AC condenser at the lower front end of the vehicle makes it susceptible to road debris, collision damage and inadequate heat exchanging from bent/damaged/plugged cooling fins or restricted airflow. The space between the condenser and radiator often fills with debris that can impede airflow and can be a source of condenser corrosion.
The expansion device of the automotive AC system will fall into two categories: with an expansion valve or with an orifice tube. Both devices separate the high-pressure and low-pressure sides of the AC system by creating a restriction. The expansion valve receives high-pressure filtered and dried refrigerant from the filter/drier and is often mounted directly to the evaporator. The expansion valve has a moving pintle that will control the amount of refrigerant sprayed into the evaporator, control the pressure drop across the system and control the evaporator output temperature.
The orifice tube has no moving parts and is used on accumulator AC systems. The orifice tube assembly is a carefully designed restriction with no moving parts. It has an inlet and outlet filter and a small, precisely designed, internal hollow tube, which allows the refrigerant to flow through it. Typically made of plastic, the orifice tube will allow the high-pressure liquid refrigerant to flow through it and expand. But unlike the expansion valve, the orifice tube cannot regulate refrigerant flow.
Expansion valve failures will result in poor AC performance. The expansion valve can stay full or partially closed, not allowing enough refrigerant to flow, causing a warm evaporator. Or it could stay fully open and allow too much refrigerant flow, causing the evaporator to freeze or ice up. Warm air blowing from the vents or frost on the vents can be indicators of a malfunctioning expansion valve. If the AC system has experienced any internal mechanical issue or failure that will allow debris — corrosion, compressor damage or desiccant bag failure, for example — the first place that the debris will show up is in the plugging of an orifice tube or the restriction on an expansion valve. Expansion valve replacement is the only fix if it is contaminated. And in a perfect world, the orifice tube should be changed when a major component — compressor, condenser, evaporator or accumulator — is changed. Neither the expansion valve nor the orifice tube should be in the system if the AC system is being flushed.
The evaporator allows the refrigerant that has passed through the expansion valve or orifice tube to change states from liquid to gas as it expands inside it. This expansion creates an evaporative cooling effect and as the HVAC fan blows cabin air across the evaporator, it will absorb latent heat from that air, cooling the cabin of the vehicle.
Some start/stop-equipped vehicles may now incorporate a cold storage evaporator to deal with the warmup of interior air when the engine is shut off and the AC compressor is no longer turning. The cold storage evaporator has two distinct parts: an evaporator portion and an accumulator portion. The accumulator portion of the cold storage evaporator is equipped with a unique phase change material (PCM). When the engine is running and the AC compressor is functioning, the refrigerant will flow through both portions of the evaporator and the PCM will freeze, becoming a cold accumulator. When the engine stops for an idle/stop/start event, the air flowing over the evaporator will continue to be cooled by the melting of the PCM inside the evaporator and not the flow of refrigerant. This cold storage helps maintain cabin comfort until the engine restarts. And when it does restart, the compressor will function again and the whole process will start over, waiting for the next engine off cycle.
The most common evaporator failure is a refrigerant leak caused by corrosion. But they can also become clogged with mold, mildew, poor cabin air filter maintenance and debris from clogged HVAC housing drains. The evaporator core needs regular maintenance by being disinfected to remove any accumulated mold and mildew. The HVAC drain needs to be kept clear of debris and regular cabin air filter maintenance is imperative. If the evaporator is being replaced because of a failure, it must have all the air deflectors, shrouding and seals that the original equipment (OE) evaporator was equipped with. These devices ensure all the air directed at the evaporator core passes through it and is not allowed to bypass around the sides, the top or the bottom of the core.
But ensuring a proper fit isn’t the only thing that needs to be looked at when replacing a failed evaporator. We need to ensure that the replacement evaporator being installed will meet or exceed the OE specification in design, function and refrigerant flow or it might not function properly and, in a worst-case scenario, need to be replaced again.
A failure of any of these four major components will result in a customer complaint of poor AC cooling performance. But careful attention to detail when diagnosing, repairing, flushing and replacing these components can lead to a seamless repair and a cool and happy customer.
Jeff Taylor boasts a 30-plus-year career in the automotive industry as a fully licensed professional lead technician. Jeff works for the CARS Training Network Inc. in Oshawa, Ontario, Canada. He is also heavily involved in government focus groups, serves as an accomplished technical writer, and he has competed in international diagnostic competitions as well as providing his expertise as an automotive technical instructor for a major aftermarket parts retailer.
About the Author
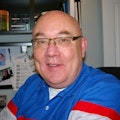
Jeff Taylor
Jeff Taylor is a seasoned professional at CARS Inc. in Oshawa with 40 years in the automotive industry. As a skilled technical writer and training developer, he holds licenses in both automotive and heavy-duty vehicle repair. Jeff excels in TAC support, technical training, troubleshooting, and shaping the future of automotive expertise.