Content brought to you by PTEN. To subscribe, click here.
With our fleet at Griffin Pavement Striping, we have more than our share of mechanical, electrical, liquid propane, fuel, hydraulic, pneumatic, or human-related failures to overcome daily, or more accurately, hourly. We have vehicles in our fleet ranging from light duty trucks to medium duty and Class 8 tractors and trailers, plus our specialized vocational equipment, both truck-mounted and stand-alone.
At first glance, our removal and application vehicles can be complex, mobile manufacturing platforms. Many of these vehicles have all the above-mentioned systems. A few even have auxiliary powerplants with vehicle-mounted air compressors to supply the additional electrical, hydraulic, or pneumatic needs that specific vehicles require to perform their tasks.
We constantly have to address more than one catastrophic issue at a time. What works best for us is breaking failures down into the core systems involved and working forwards or backward to the failure site.
We have taken the steps and invested in being as self-reliant as possible where maintaining and repairing our fleet vehicles are concerned.
The problem
What we are working with in this case is the replacement of a cylinder head on our oldest thermoplastic application striper.
The chassis is a 2007 American LaFrance Condor with a Caterpillar C11 ACERT powerplant. Our operators had been complaining of a loud ticking noise along with noticeable charring around the back cylinder bolts for the exhaust manifold.
Once we verified the location, our technicians shut off the main disconnect at the batteries. Then using his GEARWRENCH SAE 9/16” combination wrench he disconnected the cables from the positive leads. Grabbing a drain pan and a set of Channellock slip joint water pump pliers, he loosened the radiator drain valve and drained the coolant about halfway down.
The technicians then proceeded to use 3/8” and 1/2” Milwaukee M18 Fuel impacts with SK Tools and Snap-on shallow, semi-deep, and deep sockets with extensions as needed to remove the turbo and evacuate the A/C system with our Robinair 32700Z recovery machine.
From there, they removed the A/C compressor and alternator with all associated hoses, wiring, and lines for access to the exhaust manifold.
With all the accessories out of the way, access to the manifold was much better. Grabbing the Milwaukee M18 Fuel 3/8” impact, they removed all the bolts and nuts holding it on. Once we removed the manifold for inspection, we found studs broken off flush with the head surface at the front and rear exhaust ports.
We got lucky with two out of the three broken studs and were able to remove them using the Snap-on and Irwin bolt extractor sets, relatively easily. The last one... not so much. When drilling out the remaining stud, we went just a bit too far and got into the oil galley. No fixing that. We made the decision to replace the cylinder head since the unit could not cost-effectively be easily replaced and is still very much capable for use in the field.
We drained the remaining coolant and removed the intake piping, coolant hoses, serpentine belt and tensioner, cooling fan blade, and fan clutch assembly, which was bad (it was spinning freely) and the accessory bracket, which was found to be cracked. We decided it was the best time to replace the radiator and A/C condenser as well since they were original and in poor shape once we inspected them more closely.
Next, the techs removed the intake manifold, valve cover, injectors, harnesses, tappet rack, rails, and push rods. Removal of the cylinder head was fairly straightforward once we figured out the best way to support it using a fork truck and loggers chain with assistance from a 48” Mayhew prybar. Once on the bench, we removed all remaining components that would be transferred to the remanufactured cylinder head.
We found clips and a few other items that will need to be replaced as well. No surprise, honestly, since the vehicle is our oldest and we have never had reason to be into the engine this deep prior to this failure.
Our techs prepared the cylinder block surfaces with their Chicago Pneumatic angle die grinder with surface prep discs and a Cornwell straight razor blade scraper. Then we took the time to clean off the tops of the pistons and inspect the cylinder liner walls. The liners still have crosshatch, which we made sure to point out to our field crews as an example of why we perform maintenance the way we do, choosing synthetic fluids with routine fluid analysis to prolong our equipment’s lifespan.
Assembling the replacement cylinder head, tappet rack, and related harnesses on the bench, the techs chased most of the fasteners and bolt holes with Snap-on taps and dies prior to assembly. One tech placed the new head gasket on the block, and we lowered the new head into place.
Then we applied either sealant or lubricant as required to start the torque sequences for the new cylinder head bolts. Several steps and angles were involved to get through the different lengths and sizes of new bolts. Fortunately, one of our techs had purchased a Snap-on 1/2” digital torque wrench with an angle meter. We went through the process twice making sure we followed the diagrams and directions we found on Google and YouTube.
Pushrods came next, and with a Snap-on 3/8” digital torque wrench, we started snugging up the rocker arms and tappets. We followed the valve clearance adjustment procedure as outlined and rotated the assembly after each adjustment while rechecking clearances several times before locking down the tappets and installing the injectors, rocker, and valve covers. Afterward, we installed the manifolds, turbo, and related hoses and piping.
One of the techs drained the existing engine oil, removed the filters, and refilled it with fresh synthetic 5W40. Once the fuel system was primed it was time to hear it run.
Problem solved
It took several minutes of extended cranking before it fired off, running rough until it worked all the air out of the fuel system. Once that worked itself out, it ran smoothly and, most importantly, quietly. We let it run for several minutes to get some heat to build up before we took the time to remove the valve and rocker covers to recheck the valve clearances one last time.
Our techs installed a new condenser, radiator with isolator bushings, accessory mounting plate, cooling fan blade, fan hub with clutch, alternator, A/C compressor, and, finally, the serpentine belt and new tensioner.
After adding water to the cooling system, we fired it off once more and let it build to operating temperature, checking for any sign of leaks, and listening for anything that didn’t sound happy. Our process is to run it this way, with only water in the system, and to use our Pittsburgh coolant pressure tester quite a few times before we drain the system completely and fill it with extended-life coolant. This way we are likely to catch any leaks without losing much expensive coolant.
Once filled with coolant, we let it run for about 45 minutes, performing a vacuum and leak test on the A/C system using our Robinair 32700Z machine again before charging it up to capacity.
Last in the process is to road test the unit and feel for any vibrations or loss of power that could indicate there are other items needing to be addressed. This one passed without additional attention needed.
Tools used:
- Snap-on 1/2” electronic torque/angle wrench
- Feeler gauges
- Snap-on stud extractor set
- Milwaukee M18 Fuel 3/8” and 1/2” cordless impacts
- Matco Tools 3/8” cordless ratchet
- Milwaukee M18 Fuel 1/2” cordless drill
- Irwin carbide tipped drill bits
- MAC screwdrivers of varying sizes
- GEARWRENCH ratcheting wrenches
- Pittsburgh coolant system pressure tester
- Streamlight Wedge pocket flashlight
- Cornwell straight razor blade gasket scraper
- Blue Point angle tool with surface prep discs
About the Author
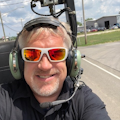
Eric Moore
Eric Moore began his career working on cars at several franchise dealerships. Initially, he leaned towards smaller vehicles, settling into Powersports vehicles, where he stayed for over 20 years. Then, Moore went the total opposite direction, landing at a medium and heavy duty truck dealership. Eventually, he moved into management and has performed most roles at the dealership level except for owning his own franchise. Currently, he is the fleet manager at Griffin Pavement Striping, belonging to the Frontline Road Safety group of companies.