According to Dictionary.com, 'outsourcing' is a verb that means "to purchase or subcontract from an outside supplier or source." The word isn't in the last paper dictionary I bought, Webster's Tenth Edition (1997). That shows how radically our spoken language and our references are changing.
Outsourcing makes a particular item, expertise or service available on an as-needed basis, so those in need don't have to spend resources on something they can purchase at lower or equal cost. Outsourcing of parts and components has existed for a long time: GM hasn't made their own car seats for decades. In more recent times companies began outsourcing business functions that used to be done in-house, like payroll or market research. Outsourcing has become very popular in the corporate world, which is how the concept got its name and became a verb at the same time.
Of course, the main motivation behind outsourcing is to reduce cost. In the 1990s, a new labor market became available to American manufacturers. That labor market was so cheap, it more than off-set increased shipping costs. Suddenly it was possible to outsource labor and drop huge savings straight to the bottom line.
In ten short years, U.S. companies outsourced almost all of their manufacturing to a culture with little manufacturing experience. They had to be taught everything, but they learned. They also learned to maximize their own profits by purchasing lower-cost raw materials and pocketing the difference, or running a third shift to produce their own products using their own raw materials but their corporate client's design and tooling. They learned other things too, but these are the only two I've heard right from the (corporate) horse's mouth.
After years of on-going quality and accountability issues, some companies are starting to bring at least part of their manufacturing back to the 'States. Others are looking for less-troublesome low-cost labor markets. These actions are motivated partly by cost issues (quality control is expensive), and partly by a growing consumer backlash, not necessarily over all products, but it's definitely there.
I've read about this backlash in news magazines, but I've also seen it myself. Recently a customer on a tool truck I was visiting complained about the quality of tools made in China and flatly refused to buy them. I myself bought Chinese-made brake drums that weren't finished properly and wouldn't fit around the backing plate, but since it was an older car, I could find no other source for that part. The new drums had to be machined before they could be installed.
After more than a decade of experience with the products made with outsourced manufacturing, techs and shop owners are saying right out loud that they're willing to pay for quality and reliability. To your customers, the words "Made in USA" means more than just jobs.
About the Author
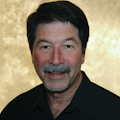
Jacques Gordon
Jacques Gordon is the former editor-in-chief of PTEN and Professional Distributor magazines. His background includes 10 years as an automotive technician and 10 years in Tier 1 suppliers’ engineering labs testing gaskets, fuel injection systems and emission control systems.
He continues to stay abreast of the latest technical developments through editorial research and technician training seminars. He holds an ASE Master Technician with L1 Certification and a Master Hybrid Technician certification from ACDC.
Jacques has been writing for aftermarket magazines since 1998, and he has earned a reputation as one of the best technical writers in the business. He is a winner of two American Society of Business Press Editor awards and several company editorial awards.
He is currently the video script writer for the CARS Training Network in Ontario, Canada.
Connect with him on LinkedIn.